Tool bits for turning CPVC
-
- Posts: 79
- Joined: Tue Sep 16, 2008 7:20 pm
- Please enter the next number in sequence: 1
- Location: Winter Haven, Florida USA
Tool bits for turning CPVC
Good evening.
I would like to try my hand at making whistles along the lines of the Water Weasel. I have a metal lathe and can grind tool bits for turning down and boring out steel. I'm curious what the tool needs to look like for turning CPVC. Can someone offer some advice please?
Thank you.
RVC
I would like to try my hand at making whistles along the lines of the Water Weasel. I have a metal lathe and can grind tool bits for turning down and boring out steel. I'm curious what the tool needs to look like for turning CPVC. Can someone offer some advice please?
Thank you.
RVC
- Feadoggie
- Posts: 3940
- Joined: Mon Feb 14, 2005 11:06 pm
- antispam: No
- Location: Stout's Valley, PA, USA
Re: Tool bits for turning CPVC
I make PVC and CPVC whistles as well as in other materials. I use standard off-the-shelf commercial bits with carbide tiips made for cutting steel and they work fine generally provided they are sharp. The usual right hand or left hand profiles work depending on how you are cutting the material. My boring bits also off-the-shelf models. I really do not use anything special. I do have a set of indexable bits that use TiN coated inserts.
I've ground my own bits as well but the commercial bits are affordable and work quite well so I'd rather spend my time turning whistle tubes instead of grinding bits. The plastics I use do not wear the bits very fast so they last a long time before they need a touch up. You'll just have to determine the proper rpm and feed rate for each bit that you use. That can result in a little waste pile of plastic but you'll zero in on what works quickly enough.
You want to keep as little bit in contact with the plastic as possible, just the cutting edge, so you want good relief all around. PVC heats up fast and will distort and melt if you go too slow or cut too deep. Be mindful of the fumes. You'll know you have things right when the swarf comes off in long, continuous spiral threads of plastic.
I've made several hundred CPVC whistles and it is a good material to work with IMO. Most PVC available in hardware stores has a lower tolerance for heat so be warned that it melts quicker than the CPVC pipe.
What's your lathe?
Feadoggie
I've ground my own bits as well but the commercial bits are affordable and work quite well so I'd rather spend my time turning whistle tubes instead of grinding bits. The plastics I use do not wear the bits very fast so they last a long time before they need a touch up. You'll just have to determine the proper rpm and feed rate for each bit that you use. That can result in a little waste pile of plastic but you'll zero in on what works quickly enough.
You want to keep as little bit in contact with the plastic as possible, just the cutting edge, so you want good relief all around. PVC heats up fast and will distort and melt if you go too slow or cut too deep. Be mindful of the fumes. You'll know you have things right when the swarf comes off in long, continuous spiral threads of plastic.
I've made several hundred CPVC whistles and it is a good material to work with IMO. Most PVC available in hardware stores has a lower tolerance for heat so be warned that it melts quicker than the CPVC pipe.
What's your lathe?
Feadoggie
I've proven who I am so many times, the magnetic strips worn thin.
-
- Posts: 79
- Joined: Tue Sep 16, 2008 7:20 pm
- Please enter the next number in sequence: 1
- Location: Winter Haven, Florida USA
Re: Tool bits for turning CPVC
Thanks very much. I have an old Enco 9x20 which should be sufficient for the job.
If you don't mind another question, what material do you use for the fipple block? I figure CPVC would be a good choice as solid 1/2" rod is readily available on-line. Will that work or would you suggest another material?
I appreciate your help.
RVC
If you don't mind another question, what material do you use for the fipple block? I figure CPVC would be a good choice as solid 1/2" rod is readily available on-line. Will that work or would you suggest another material?
I appreciate your help.
RVC
- Feadoggie
- Posts: 3940
- Joined: Mon Feb 14, 2005 11:06 pm
- antispam: No
- Location: Stout's Valley, PA, USA
Re: Tool bits for turning CPVC
The Enco 9x20 should do just fine.
Let us know how things turns out!
Feadoggie
I've used most every material I could experiment with including delrin, acetal, nylon, CPVC, PVC, HDPE, acrylic, polycarbonate, cast resins, plastic clays, various woods and more. Each has their own puts and takes. Nowadays I use delrin for some whistles and PVC for others. What I like about those two materials is that they machine cleanly and can easily be finished to a smooth polish. CPVC rod works very much the same as PVC. The PVC/CPVC rod has the advantage that it can be glued. But I still pin all my heads anyway. PVC/CPVC rod is readily available at most local plastics suppliers and as you say it's available online. It's also a lot less expensive than delrin or acetal. There's no reason not to use CPVC that I have found. I have used PVC plugs for about ten years now and it has held up just fine. I just purchased another 50' of PVC a couple weeks ago so I guess I am committed to using it for some time down the road.RVC wrote:what material do you use for the fipple block? I figure CPVC would be a good choice as solid 1/2" rod is readily available on-line. Will that work or would you suggest another material?
Let us know how things turns out!
Feadoggie
I've proven who I am so many times, the magnetic strips worn thin.
-
- Posts: 79
- Joined: Tue Sep 16, 2008 7:20 pm
- Please enter the next number in sequence: 1
- Location: Winter Haven, Florida USA
Re: Tool bits for turning CPVC
Thank you, sir. I look forward to starting on this. I'll let you know how it turns out - maybe a picture or two as well.
RVC
RVC
-
- Posts: 79
- Joined: Tue Sep 16, 2008 7:20 pm
- Please enter the next number in sequence: 1
- Location: Winter Haven, Florida USA
Re: Tool bits for turning CPVC
I trust it's not too late to resurrect this thread with a follow-up post. I've been working on my "waste pile of plastic" here and probably will continue for a few more tries. A couple questions have arisen.
I am currently shooting for the wall thickness for the inner and outer parts to be one half the total wall thickness each. Without wanting anyone to divulge trade secrets, is that about right? If not what thickness of each part should I aim at?
I have heard there are specific types of files to use to file the ramp. What are they called and where can they be obtained?
Thank you.
RVC
I am currently shooting for the wall thickness for the inner and outer parts to be one half the total wall thickness each. Without wanting anyone to divulge trade secrets, is that about right? If not what thickness of each part should I aim at?
I have heard there are specific types of files to use to file the ramp. What are they called and where can they be obtained?
Thank you.
RVC
- Feadoggie
- Posts: 3940
- Joined: Mon Feb 14, 2005 11:06 pm
- antispam: No
- Location: Stout's Valley, PA, USA
Re: Tool bits for turning CPVC
It's never too late. Almost like we're open all night, well somewhere on earth there's usually a whistle maker up, awake and willing to offer assistance.RVC wrote:I trust it's not too late to resurrect this thread with a follow-up post. I've been working on my "waste pile of plastic" here and probably will continue for a few more tries. A couple questions have arisen.
Keeping in mind the venerable Water Weasel as the model - there are two places on the whistle where you make a tenon and socket joint.RVC wrote:I am currently shooting for the wall thickness for the inner and outer parts to be one half the total wall thickness each. Without wanting anyone to divulge trade secrets, is that about right? If not what thickness of each part should I aim at?
The tuning slide is a matter of structure mostly. But you'd rather not have the tenon half too thick so as to create much of a bore expansion at the point where the joint opens in the whistle bore. So make the tenon just thick enough to be stable and durable. How much is up to you actually. If you split the difference with the socket half it will still work. Insert a spare piece of plug material in the bore when you are turning the tenon down to support the plastic from the inside when as you make it thinner.
The thickness of the tenon at the mouthpiece end of the head is all about the desired windway height. The thicker the tenon, the more height there will be to the windway. That will effect the voice and breath of the finished whistle. If you split the difference between the inner and outer mouthpiece my feeling is that you will get a windway that is too narrow. But keep in mind that that is just my opinion. So I favor a thicker tenon and thinner socket. I'll not give you my measurement marks here but you will figure things out.
Here's a shop tip for boring out the plastic for the outer mouthpiece. It is not simple to bore the outer mouthpiece to the desired thickness on its own. First of all there is no need to cut a short piece of plastic just for that part. You can bore the part to depth on a longer piece of stock which can be mounted through the spindle and part it off when the boring is done. To support the tube on the outside while boring you can chuck it in a sacrificial piece of Sched 40 PVC cold water pipe or grey PVC conduit. The PVC pipe happpens to have a similar inside diameter as the outside diameter of the ivory CPVC. Make a cut with a hacksaw across the PVC pipe so it clamps the CPVC as you tighten the chuck around it. That will give you the support you need to make the CPVC thin enough to fit over the head tenon.
If that's not clear, I could maybe take a picture later.
Files are a mater of personal taste too. I rough cut the blade with a small square wood rasp. Then I use jeweler files to finish. You can easily get away with a set of inexpensive needle files from a supplier like Harbor Freight. They are on sale today! I know. I just came home from H-F and my son bought a set of twelve needle files for like $3. They will work well enough. I have a few dozen of those but what I prefer to use are 4" long Swiss made, Swiss pattern jeweler's files. They are available from online jeweler supply shops. They are not cheap. The difference between the cheap files and the expensive files is the uniformity and sharpness of the cutting surface. The cheap ones do not cut as fast as the more expensive ones. The cheap ones load up with plastic or metal and need to be cleaned more frequently. That is not too difficult to handle. But the expensive ones seem to cut a finer surface that needs less polishing and such to finish it up.RVC wrote:I have heard there are specific types of files to use to file the ramp. What are they called and where can they be obtained?
And you can read the discussion here: viewtopic.php?f=1&t=44414
Feadoggie
I've proven who I am so many times, the magnetic strips worn thin.
-
- Posts: 79
- Joined: Tue Sep 16, 2008 7:20 pm
- Please enter the next number in sequence: 1
- Location: Winter Haven, Florida USA
Re: Tool bits for turning CPVC
Thanks again for you reply and the info therein. Especially thanks for the link. The other guys and gals were right - you make beautiful whistles.
My thought about the half and half approach came from observing a picture of an Eb Water Weasel on the Wandering Whilstler archive. The end photo of the mouthpiece looked at first glance to be about half and half. Now that you mention it, though, it does appear the inner piece has a little thicker wall thickness so I'll head that way.
Excellent shop tip! I assume your saw cut is with the length of the PVC? I'll give it a try but a greater problem at present is with the inner piece. It generally ends up being a few thousandths greater in diameter at the end than the material closer to the chuck. I assume it is deflecting slightly when the cutting tool meets it and the deflection decreases as the cut moves toward the chuck. I was thinking about trying to come up with a steel rod to fit fairly snuggly on the inside of the CPVC and extend back through the jaws of the chuck. Is that similar to how you handle that problem if you have it at all?
Thanks again for the excellent info.
RVC
My thought about the half and half approach came from observing a picture of an Eb Water Weasel on the Wandering Whilstler archive. The end photo of the mouthpiece looked at first glance to be about half and half. Now that you mention it, though, it does appear the inner piece has a little thicker wall thickness so I'll head that way.
Excellent shop tip! I assume your saw cut is with the length of the PVC? I'll give it a try but a greater problem at present is with the inner piece. It generally ends up being a few thousandths greater in diameter at the end than the material closer to the chuck. I assume it is deflecting slightly when the cutting tool meets it and the deflection decreases as the cut moves toward the chuck. I was thinking about trying to come up with a steel rod to fit fairly snuggly on the inside of the CPVC and extend back through the jaws of the chuck. Is that similar to how you handle that problem if you have it at all?
Thanks again for the excellent info.
RVC
- Feadoggie
- Posts: 3940
- Joined: Mon Feb 14, 2005 11:06 pm
- antispam: No
- Location: Stout's Valley, PA, USA
Re: Tool bits for turning CPVC
Yes, that's right. Taking out just the width of the kerf of the saw blade is enough to be able to clamp the work piece once chucked up so that you can bore it out without spinning against the boring bit or deflecting out of round.RVC wrote: I assume your saw cut is with the length of the PVC?
I can chuck the CPVC and turn the Inner/tenon portion of the mouthpiece without inserting the plug to stiffen the CPVC tube. Sharp bits, conservative depth of cut, good rpm and non-aggressive feed rates and multiple passes should work. Of course I created a pile of useless plastic before I got things right.RVC wrote:a greater problem at present is with the inner piece. It generally ends up being a few thousandths greater in diameter at the end than the material closer to the chuck. I assume it is deflecting slightly when the cutting tool meets it and the deflection decreases as the cut moves toward the chuck. I was thinking about trying to come up with a steel rod to fit fairly snuggly on the inside of the CPVC and extend back through the jaws of the chuck. Is that similar to how you handle that problem if you have it at all?
You should be able to tell if you are pushing the material instead of cutting. The plastic will get warm. You definitely do not want to smell CPVC when you are turning it. If you do, you are probably being too aggressive. But what you describe is surely what is occurring.
The solid rod inserted in the tube whether it is steel or delrin, which I use, will help keep things stiffer. Proceed just as you described. You could also use a rolling follower rest as well. But the stiffening rod should be enough. You're only working about an inch and a half, at most, from the chuck. So just go slow and turn a little off at a time. I generally take at least five passes to turn off the excess material from the outside of the mouthpiece tenon.
Work safe and have fun!
Feadoggie
I've proven who I am so many times, the magnetic strips worn thin.
-
- Posts: 562
- Joined: Thu Feb 07, 2008 3:30 pm
- antispam: No
- Please enter the next number in sequence: 12
- Location: Ohio
Re: Tool bits for turning CPVC
I concur with all Feadoggie has said and would add a couple extra points:
I use turning tools with inserts - for making tenons I do not usually insert rod - I have in the past, and it does work however the ids of the tubes vary necessitating custom turned rods - though you can reuse the rod for your fipple! - several passes (5 does sound about right) with the last two being very light, and I also find the TAR turning tool with a 0° lead angle ( I think that is what is called) pushes the plastic in less.
Boring is easy since I use er32 collet chuck and they completely support the tube. I have in the past slipped brass tubing with an id of 0.625 over the tube, but its a bother and is sometimes hard to get back off.
As to files and making ramps I just have some cheap files (I'm sure some good ones would be worth the $ but I don't use that much), I used to rough cut the ramp with an end mill and then shape, then I made a cutter that would cut a curved ramp which required very little touch up but the cutter was hard to set up and hard to use. I now do it differently and turn my 'labiums' on the lathe and then insert into the head - this seems much more repeatable and controllable.
Windway height is very important (in that small changes can be important) and it depends on the sound you want and on the rest of the head design as well. I'm with Feadoggie here too, I'm not going to give you a number and if I did it would probably be wrong for your whistle, but I will say that half of the wall thickness is probably too small and the whole wall thickness works but is breathy and not too efficient - my first whistle just used a piece of the aforementioned 0.625 id brass tube to form the top or ceiling of the windway, it works and is simple but I only made two whistles that way. And I will add that after making quite a few whistles I'm still playing with the windway height - as Guido says on his site 0.1mm makes a difference (I would add: a very noticeable difference).
It is a slippery slope, have fun, work safe, and let us know how you do.
I use turning tools with inserts - for making tenons I do not usually insert rod - I have in the past, and it does work however the ids of the tubes vary necessitating custom turned rods - though you can reuse the rod for your fipple! - several passes (5 does sound about right) with the last two being very light, and I also find the TAR turning tool with a 0° lead angle ( I think that is what is called) pushes the plastic in less.
Boring is easy since I use er32 collet chuck and they completely support the tube. I have in the past slipped brass tubing with an id of 0.625 over the tube, but its a bother and is sometimes hard to get back off.
As to files and making ramps I just have some cheap files (I'm sure some good ones would be worth the $ but I don't use that much), I used to rough cut the ramp with an end mill and then shape, then I made a cutter that would cut a curved ramp which required very little touch up but the cutter was hard to set up and hard to use. I now do it differently and turn my 'labiums' on the lathe and then insert into the head - this seems much more repeatable and controllable.
Windway height is very important (in that small changes can be important) and it depends on the sound you want and on the rest of the head design as well. I'm with Feadoggie here too, I'm not going to give you a number and if I did it would probably be wrong for your whistle, but I will say that half of the wall thickness is probably too small and the whole wall thickness works but is breathy and not too efficient - my first whistle just used a piece of the aforementioned 0.625 id brass tube to form the top or ceiling of the windway, it works and is simple but I only made two whistles that way. And I will add that after making quite a few whistles I'm still playing with the windway height - as Guido says on his site 0.1mm makes a difference (I would add: a very noticeable difference).
It is a slippery slope, have fun, work safe, and let us know how you do.
“When a Cat adopts you there is nothing to be done about it except put up with it until the wind changes.” T.S. Elliot
-
- Posts: 79
- Joined: Tue Sep 16, 2008 7:20 pm
- Please enter the next number in sequence: 1
- Location: Winter Haven, Florida USA
Re: Tool bits for turning CPVC
Thanks again for your help, gentlemen. I didn't expect exact measurements as I alluded to in my first post. I realize those are hard-won figures that deserve to remain proprietary. Besides they probably wouldn't work for me anyway.
Fortunately I have a copy of Glenn Shultz's article in The Woodwind Quarterly #8 which gives me a lot going in. That and your info add to it, and so now it's back to the lathe to make more pieces of plastic. Good thing CPVC is cheap.
Your help is most appreciated.
RVC
Fortunately I have a copy of Glenn Shultz's article in The Woodwind Quarterly #8 which gives me a lot going in. That and your info add to it, and so now it's back to the lathe to make more pieces of plastic. Good thing CPVC is cheap.
Your help is most appreciated.
RVC
Re: Tool bits for turning CPVC
A wind way hight of half the thickness of the tube wall is a fair place to start. Going down to about .047'' or less makes a pure sound. Depending on how much moisture a player generates a smaller wind way hight could have clogging. WW hight above about .050 and it will sound more airy. Some players like a little airy.
Between .0468 and .0625 will work. Then it will depend on the bevel at the end of the plug. One way to make a plug is to put a cross mark on the end and leave one section of the pie with no bevel and the other three with progressively a little more bevel on each. Insert the plug without cutting the underside of the head for the lower lip. Now the plug can be rotated to a different bevel and also moved in and out to study the effects of each bevel and distance from the end of the plug to the ramp.
Whistles with wood head sleeves seem to me to have less clogging. They are no more difficult to make than a cpvc sleeve.

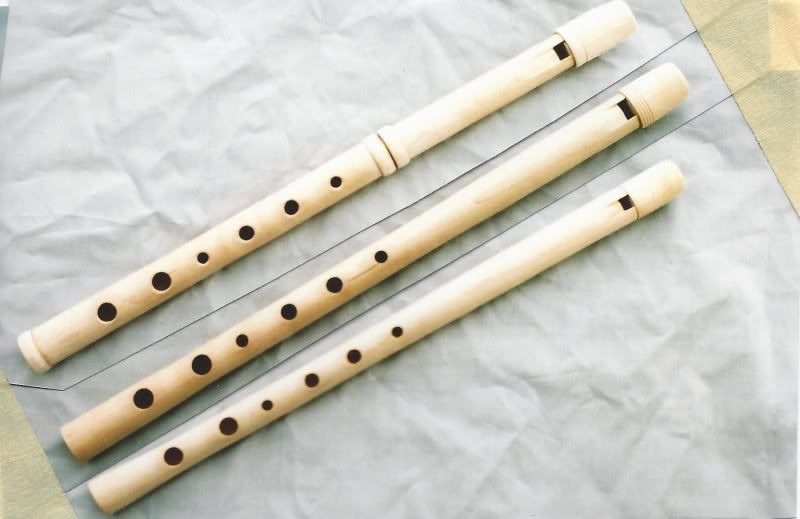
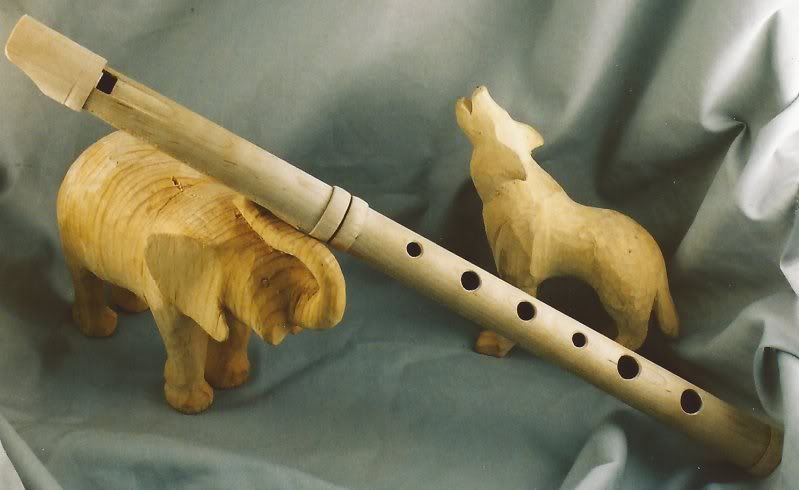
OK hecklers be careful with the flame on. There is dry wood about.

Between .0468 and .0625 will work. Then it will depend on the bevel at the end of the plug. One way to make a plug is to put a cross mark on the end and leave one section of the pie with no bevel and the other three with progressively a little more bevel on each. Insert the plug without cutting the underside of the head for the lower lip. Now the plug can be rotated to a different bevel and also moved in and out to study the effects of each bevel and distance from the end of the plug to the ramp.
Whistles with wood head sleeves seem to me to have less clogging. They are no more difficult to make than a cpvc sleeve.

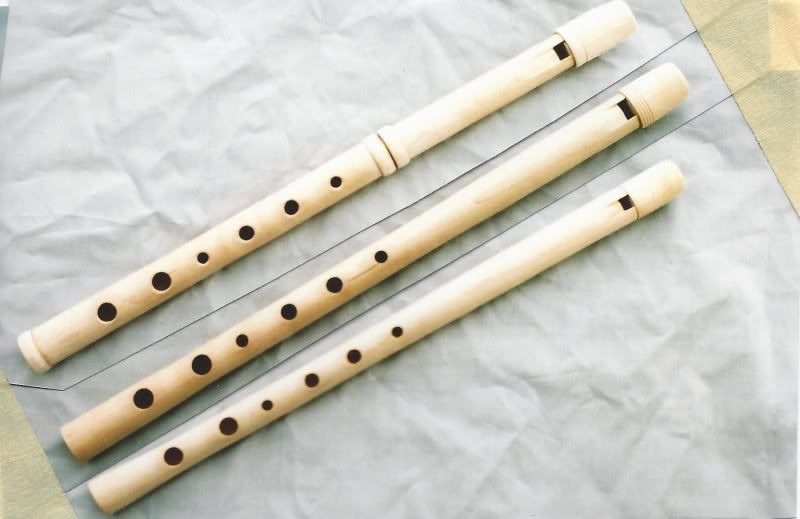
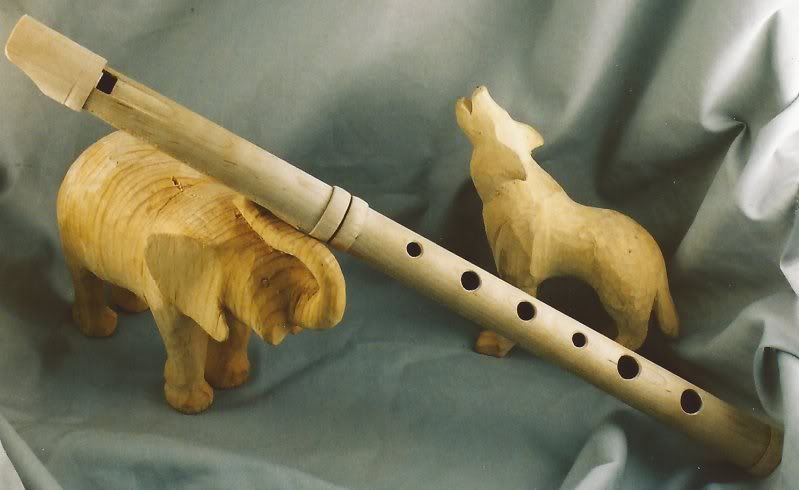
OK hecklers be careful with the flame on. There is dry wood about.


''Whistles of Wood'', cpvc and brass. viewtopic.php?f=1&t=69086
- Feadoggie
- Posts: 3940
- Joined: Mon Feb 14, 2005 11:06 pm
- antispam: No
- Location: Stout's Valley, PA, USA
Re: Tool bits for turning CPVC
RVC, highwood makes a couple really good points that I overlooked earlier. The inside diameter of CPVC pipe does vary. Oddly enough, it is the outside outside diameter that is standardized. So yes, one plug will not fit every piece of pipe that you chuck up in the lathe. But I do find that the diameter of a 10' piece of pipe is fairly consistent, at least in my experience. So you don't have to make a custom plug to stiffen each piece really. I have a small plastic can of scrap plugs on the bench to draw from. But if you make the fipple plug before you turn the mouthpiece tenon you will have killed two birds with one stone. You'll have a custom stiffener plug and the final fipple plug. I'd suggest you make the plug a couple millemeters long to start. That way it will support the CPVC for turning a little beyond the cut. You can trim the excess after you've fit the plug for voicing.
Collet, that's the word I looking for! The PVC sleeve I described above is just a poor man's collet. Highwood is fortunate to have the ER32 collet set. (A collet set and collet chuck is on my "want list".) Collets are the best way to hold round stock firmly without distorting its shape. When you turn a piece of CPVC mounted in a three (or four or even six) jaw chuck, the pressure on the outside of the material is greater at the points where the ckuck jaws contact the material. At some point as you bore out material for a socket the pipe will change shape making the cut chatter or let the material spin. So you want to avoid that if you can. A collet is the way to go. It distributes the clamping forces uniformly around the pipe.
Highwood also mentions using .625 i.d. brass tube as a mouthpiece collar. K&S brass tubing is available in an array of nesting/telescoping sizes. You can use parted off pieces the .625 tubing as both rings of mouthpiece fittings as options. Other sizes make good tuning slides.

But you could also experiment with smaller diameters as well. K&S tubing is sized by its outside diameter and available from hobby and craft shops as well as online. The K&S 21/32 i.d. tube has an inside diameter of ~5/8" and usually slips over CPVC pipe just fine. The next size down, 5/8", has an i.d. of about 19/32". That makes rings and mouthpieces that will fit flush with the PVC.

If you find that makes a whistle that is too breathy you can try the 19/32" o.d. and so on. You could also experiment by using copper water pipe in a similar manner.
As I've said before, make a few hundred of these and you'll have things figured out.
Feadoggie
Collet, that's the word I looking for! The PVC sleeve I described above is just a poor man's collet. Highwood is fortunate to have the ER32 collet set. (A collet set and collet chuck is on my "want list".) Collets are the best way to hold round stock firmly without distorting its shape. When you turn a piece of CPVC mounted in a three (or four or even six) jaw chuck, the pressure on the outside of the material is greater at the points where the ckuck jaws contact the material. At some point as you bore out material for a socket the pipe will change shape making the cut chatter or let the material spin. So you want to avoid that if you can. A collet is the way to go. It distributes the clamping forces uniformly around the pipe.
Highwood also mentions using .625 i.d. brass tube as a mouthpiece collar. K&S brass tubing is available in an array of nesting/telescoping sizes. You can use parted off pieces the .625 tubing as both rings of mouthpiece fittings as options. Other sizes make good tuning slides.

But you could also experiment with smaller diameters as well. K&S tubing is sized by its outside diameter and available from hobby and craft shops as well as online. The K&S 21/32 i.d. tube has an inside diameter of ~5/8" and usually slips over CPVC pipe just fine. The next size down, 5/8", has an i.d. of about 19/32". That makes rings and mouthpieces that will fit flush with the PVC.

If you find that makes a whistle that is too breathy you can try the 19/32" o.d. and so on. You could also experiment by using copper water pipe in a similar manner.
As I've said before, make a few hundred of these and you'll have things figured out.

Feadoggie
I've proven who I am so many times, the magnetic strips worn thin.
-
- Posts: 562
- Joined: Thu Feb 07, 2008 3:30 pm
- antispam: No
- Please enter the next number in sequence: 12
- Location: Ohio
Re: Tool bits for turning CPVC
Not really when you think about it - it needs to fit the connectorsOddly enough, it is the outside outside diameter that is standardized.
They weren't cheap but I love them makes many things much easier, faster and more accurate.A collet set and collet chuck is on my "want list"
Ditto all the comments on K&S tubing - which is also very consistent both id and od.
“When a Cat adopts you there is nothing to be done about it except put up with it until the wind changes.” T.S. Elliot
-
- Posts: 79
- Joined: Tue Sep 16, 2008 7:20 pm
- Please enter the next number in sequence: 1
- Location: Winter Haven, Florida USA
Re: Tool bits for turning CPVC
I appreciate all the input to this point and the insight gained from it. It's clear that my first task will be to master the art of accurately machining CPVC and there is more involved to it than I originally thought. Not surprising I suppose and I'm looking forward to the learning curve. I'll probably concentrate on making a whistle work using just the CPVC and consider moving on to trying brass down the road.
I went down to my local Lowe's to buy a new supply of pipe and discovered they don't carry the FlowGuard Gold by Charlotte Pipe anymore. Now they have Silver-Line Ultra-Pure. It has the same ASTM number so I guess it's the same pipe, although it has blue printing instead of the neat black printing on a yellow background which I much prefer. Silly reason to prefer one pipe over another I guess.
Thanks for the numbers, Tommy, and for the pictures. What kind of wood is that? Looks like maple.
Once again, I appreciate all the insight.
RVC
I went down to my local Lowe's to buy a new supply of pipe and discovered they don't carry the FlowGuard Gold by Charlotte Pipe anymore. Now they have Silver-Line Ultra-Pure. It has the same ASTM number so I guess it's the same pipe, although it has blue printing instead of the neat black printing on a yellow background which I much prefer. Silly reason to prefer one pipe over another I guess.
Thanks for the numbers, Tommy, and for the pictures. What kind of wood is that? Looks like maple.
Once again, I appreciate all the insight.
RVC