
I just (very promptly) received my box of 10 x upper joint blanks, 10 x lower joint blanks and 5 x milled bells.
The quality of this wood is very nice.
The lower joints (3 bumps) are not equal in dimensions as mentioned above. 6 of mine are 9.85" (250mm) long Bb soprano lower joints with a tenon receiver at the top and a socket at the end. The other 4 are 11" or 280mm long and probably alto clarinet lower joints with a tenon receiver at the top and just an indentation and the bottom end. Or are they for an A clarinet? I don't have an A soprano or an Alto to compare.
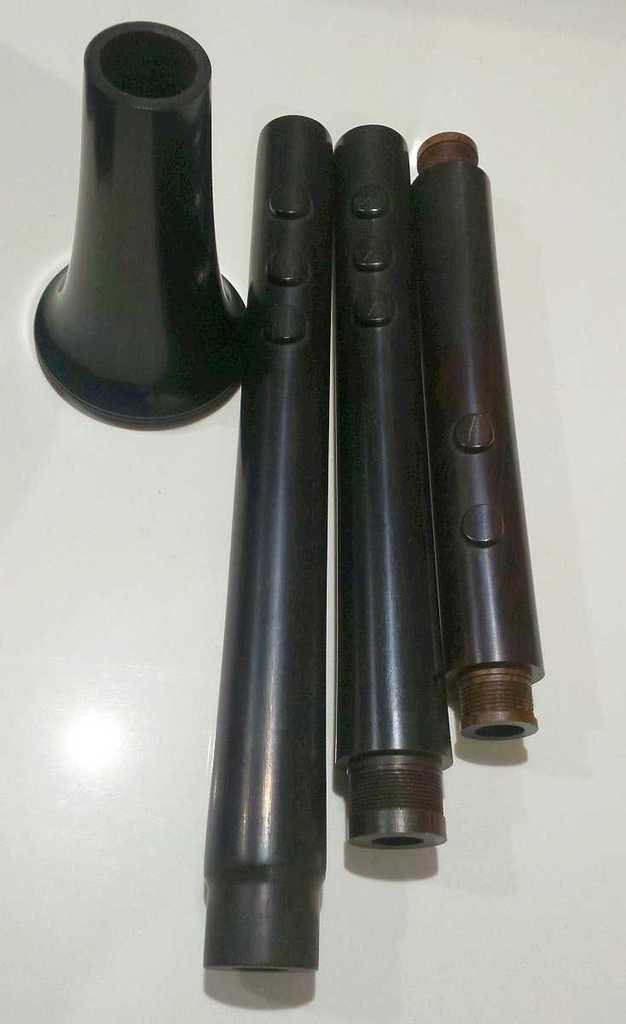
This is a super rare chance for a weekend woodturner/flutemaker to try his hand at the 'good stuff'.
Thanks to the C&F forum for letting me find the wonderful person to come to my aid and obtain these blanks.
Vaughan