This Old Flute #2 - HF Meyer
- jemtheflute
- Posts: 6969
- Joined: Tue May 23, 2006 6:47 am
- antispam: No
- Please enter the next number in sequence: 8
- Location: N.E. Wales, G.B.
- Contact:
Re: ?Genuine Meyer on eBay?
I wasn't sure whther to revive this thread or start a new one......
Anyway, this stunning beauty http://cgi.ebay.co.uk/ws/eBayISAPI.dll? ... 0315487208 is currently on eBay - from the same eBay dealer in Sofia as I bought the Norton 1-key in my avatar picture a couple of years back - reputable IMO/experience. He doesn't explain fully, but seems very certain this is a genuine Meyer despite the lack of stamps - mentions an interesting provenance story at any rate. It can be seen in the excellent photos that it is certainly a high quality flute, a cut or three above the general run of German C19th instruments. Nice bit of cocus too! Very reasonable asking price for what it is too - although it is at A=435.......
Go have a drool.........
Anyway, this stunning beauty http://cgi.ebay.co.uk/ws/eBayISAPI.dll? ... 0315487208 is currently on eBay - from the same eBay dealer in Sofia as I bought the Norton 1-key in my avatar picture a couple of years back - reputable IMO/experience. He doesn't explain fully, but seems very certain this is a genuine Meyer despite the lack of stamps - mentions an interesting provenance story at any rate. It can be seen in the excellent photos that it is certainly a high quality flute, a cut or three above the general run of German C19th instruments. Nice bit of cocus too! Very reasonable asking price for what it is too - although it is at A=435.......
Go have a drool.........
Last edited by jemtheflute on Wed Mar 18, 2009 6:47 pm, edited 1 time in total.
I respect people's privilege to hold their beliefs, whatever those may be (within reason), but respect the beliefs themselves? You gotta be kidding!
My YouTube channel
My FB photo albums
Low Bb flute: 2 reels (audio)
Flute & Music Resources - helpsheet downloads
My YouTube channel
My FB photo albums
Low Bb flute: 2 reels (audio)
Flute & Music Resources - helpsheet downloads
- Carey
- Posts: 578
- Joined: Fri Jan 19, 2007 8:38 pm
- Please enter the next number in sequence: 1
- Location: In the dog house. Gone playing music too much recently.
- Contact:
Re: This Old Flute #2 - HF Meyer
Very nice. Thanks for the heads up Jem!
When there's a huge spill of solar energy, it's just called a nice day.
http://www.parkswhistles.com
http://www.parkswhistles.com
Re: This Old Flute #2 - HF Meyer
The head at first looked to be a Boosey, but with that rectangular embouchure cut, IDK. I'll bet it sounds great for the price.
- Carey
- Posts: 578
- Joined: Fri Jan 19, 2007 8:38 pm
- Please enter the next number in sequence: 1
- Location: In the dog house. Gone playing music too much recently.
- Contact:
Re: This Old Flute #2 - HF Meyer
At long last I got out the HF Meyer and had a go at the head.
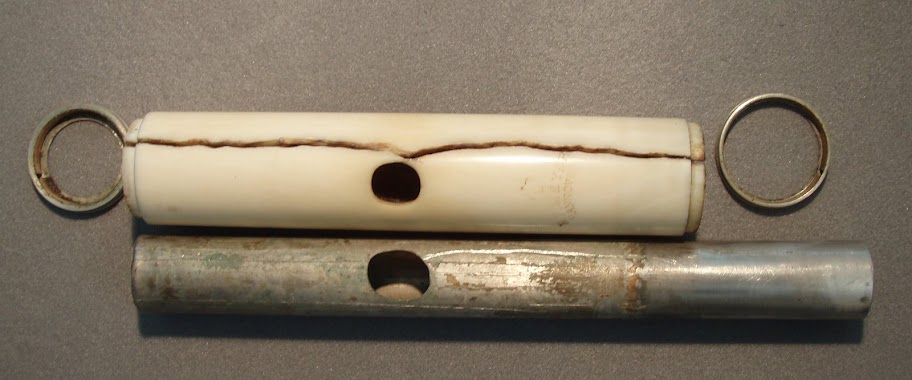
I found a couple interesting things (interesting to me having never been here before. Others will have expected it.)
First, liner was at one time a flat piece of metal that was rolled and welded or soldered into a tube.
Second, the embouchure was drilled in the liner and the ivory separately. "Cut" might be a better word in the case of the liner.
Third, the "rings" are not rings at all, but formed metal around wood or maybe ivory rings.
Fourth, there's "gunk" that may have been glue at one time holding it all together.
Fifth, it takes quite a bit of pressure to close the crack much at all. I've made a slotted PVC sleeve that fits over the ivory and I can apply pressure to the slotted sleeve to even out the pressure and avoid marking the ivory.
My current approach is to clean the gunk out of the crack and then close it up with pressure and glue it with CA glue. Then I'll enlarge the ID so the liner fits, probably with sandpaper on a stick. I'll save the sanding dust and try to cover up the crack with it.
Your thoughts and comments are welcome.
I found a couple interesting things (interesting to me having never been here before. Others will have expected it.)
First, liner was at one time a flat piece of metal that was rolled and welded or soldered into a tube.
Second, the embouchure was drilled in the liner and the ivory separately. "Cut" might be a better word in the case of the liner.
Third, the "rings" are not rings at all, but formed metal around wood or maybe ivory rings.
Fourth, there's "gunk" that may have been glue at one time holding it all together.
Fifth, it takes quite a bit of pressure to close the crack much at all. I've made a slotted PVC sleeve that fits over the ivory and I can apply pressure to the slotted sleeve to even out the pressure and avoid marking the ivory.
My current approach is to clean the gunk out of the crack and then close it up with pressure and glue it with CA glue. Then I'll enlarge the ID so the liner fits, probably with sandpaper on a stick. I'll save the sanding dust and try to cover up the crack with it.
Your thoughts and comments are welcome.
When there's a huge spill of solar energy, it's just called a nice day.
http://www.parkswhistles.com
http://www.parkswhistles.com
- jemtheflute
- Posts: 6969
- Joined: Tue May 23, 2006 6:47 am
- antispam: No
- Please enter the next number in sequence: 8
- Location: N.E. Wales, G.B.
- Contact:
Re: This Old Flute #2 - HF Meyer
So ar so good, Carey - and you're right, none of your observations surprise me save the one about the rings - and I'm not entirely sure I understand you aright on those.
Two thoughts
1) If it takes a lot of pressure to close up the crack, no matter what glue you use it will likely tear open again in the short-to-medium term at best, or crack elsewhere. You'd probably need to pin or stitch it to reduce the chance of it re-opening, and that wouldn't help at all with the risk of a new crack. You might actually be better off going the dental filler route if you can get it - unless your crack is through the embouchure - I can't recall if it is? In wood the whole point in removing the liner and enlarging the bore is to remove stresses so that a new crack is less likely, which was always the problem with and argument against drawing cracks together around an in situ liner by force with pins or "stitching". Pretty much the same applies to ivory, though with the caveat that we know that ivory tends to shrink more with time than even wood, seemingly (is why your crack won't just close after liner removal). I wonder if there is any way you can soften the ivory to allow you to close the crack with less tension - steam perhaps, or some kind of oil bath? I've wondered a couple of times about trying that with wood - I know you'd have to let it dry out again pretty thoroughly before re-reaming or reassembly, but the drying out would be rather different in nature from the historic dehydration of the material's own original moisture content. You wouldn't want to rehydrate deeply or for the long term as that would only lead to a new cycle of hygroscopic expansion and shrinkage. If you could soften the material to press the crack closed with less stress and then let it dry and harden in the new shape, that would be a big step forward. On another tack, you could perhaps try using a very fine saw blade through the bore to make some longitudinal partial thickness radial cuts from the inside along the grain - those would allow slightly less stressful crack compression without any external cosmetic effects, though I suppose they might also create candidate sites for future cracking...... (They'd be nicely filled up by Gorilla Gue if you use that for refixing the liner.)
Ultimately, if the crack is through the embouchure and won't close without undue new stress, I'd suggest pinning the crack to draw it together just a little and make it stable without too much stress, doing the bore re-ream to refit the tube, but cutting a new embouchure in a different quadrant of the tube - then fit the liner so the holes match and refix it: then use the dental filler to fill the crack AND the old embouchure hole over the liner.
Anyone know of any manuals for working ivory?
2) If you want to reserve self-dust for crack dressing, don't use sandpaper! You'll get dust with sand in it, which will show in the surface finish if you use it for dressing! Sand away any glue residue you haven't removed by other means from the bore, then, when you're on clean ivory (or wood in other cases) use a fairly fine half-round engineering metal file and reserve pure dust!
Two thoughts
1) If it takes a lot of pressure to close up the crack, no matter what glue you use it will likely tear open again in the short-to-medium term at best, or crack elsewhere. You'd probably need to pin or stitch it to reduce the chance of it re-opening, and that wouldn't help at all with the risk of a new crack. You might actually be better off going the dental filler route if you can get it - unless your crack is through the embouchure - I can't recall if it is? In wood the whole point in removing the liner and enlarging the bore is to remove stresses so that a new crack is less likely, which was always the problem with and argument against drawing cracks together around an in situ liner by force with pins or "stitching". Pretty much the same applies to ivory, though with the caveat that we know that ivory tends to shrink more with time than even wood, seemingly (is why your crack won't just close after liner removal). I wonder if there is any way you can soften the ivory to allow you to close the crack with less tension - steam perhaps, or some kind of oil bath? I've wondered a couple of times about trying that with wood - I know you'd have to let it dry out again pretty thoroughly before re-reaming or reassembly, but the drying out would be rather different in nature from the historic dehydration of the material's own original moisture content. You wouldn't want to rehydrate deeply or for the long term as that would only lead to a new cycle of hygroscopic expansion and shrinkage. If you could soften the material to press the crack closed with less stress and then let it dry and harden in the new shape, that would be a big step forward. On another tack, you could perhaps try using a very fine saw blade through the bore to make some longitudinal partial thickness radial cuts from the inside along the grain - those would allow slightly less stressful crack compression without any external cosmetic effects, though I suppose they might also create candidate sites for future cracking...... (They'd be nicely filled up by Gorilla Gue if you use that for refixing the liner.)
Ultimately, if the crack is through the embouchure and won't close without undue new stress, I'd suggest pinning the crack to draw it together just a little and make it stable without too much stress, doing the bore re-ream to refit the tube, but cutting a new embouchure in a different quadrant of the tube - then fit the liner so the holes match and refix it: then use the dental filler to fill the crack AND the old embouchure hole over the liner.
Anyone know of any manuals for working ivory?
2) If you want to reserve self-dust for crack dressing, don't use sandpaper! You'll get dust with sand in it, which will show in the surface finish if you use it for dressing! Sand away any glue residue you haven't removed by other means from the bore, then, when you're on clean ivory (or wood in other cases) use a fairly fine half-round engineering metal file and reserve pure dust!
I respect people's privilege to hold their beliefs, whatever those may be (within reason), but respect the beliefs themselves? You gotta be kidding!
My YouTube channel
My FB photo albums
Low Bb flute: 2 reels (audio)
Flute & Music Resources - helpsheet downloads
My YouTube channel
My FB photo albums
Low Bb flute: 2 reels (audio)
Flute & Music Resources - helpsheet downloads
- Jon C.
- Posts: 3526
- Joined: Wed Nov 07, 2001 6:00 pm
- antispam: No
- Please enter the next number in sequence: 8
- Tell us something.: I restore 19th century flutes, specializing in Rudall & Rose, and early American flutes. I occasionally make new flutes. Been at it for about 15 years.
- Location: San Diego
Re: This Old Flute #2 - HF Meyer
Hi,Carey wrote:At long last I got out the HF Meyer and had a go at the head.
I found a couple interesting things (interesting to me having never been here before. Others will have expected it.)
First, liner was at one time a flat piece of metal that was rolled and welded or soldered into a tube.
Second, the embouchure was drilled in the liner and the ivory separately. "Cut" might be a better word in the case of the liner.
Third, the "rings" are not rings at all, but formed metal around wood or maybe ivory rings.
Fourth, there's "gunk" that may have been glue at one time holding it all together.
Fifth, it takes quite a bit of pressure to close the crack much at all. I've made a slotted PVC sleeve that fits over the ivory and I can apply pressure to the slotted sleeve to even out the pressure and avoid marking the ivory.
My current approach is to clean the gunk out of the crack and then close it up with pressure and glue it with CA glue. Then I'll enlarge the ID so the liner fits, probably with sandpaper on a stick. I'll save the sanding dust and try to cover up the crack with it.
Your thoughts and comments are welcome.
I tried that, it didn't hold for me. Still thinking of a good fix for the problem. But maybe yours will hold, good luck!

"I love the flute because it's the one instrument in the world where you can feel your own breath. I can feel my breath with my fingers. It's as if I'm speaking from my soul..."
Michael Flatley
Jon
Michael Flatley
Jon
- Carey
- Posts: 578
- Joined: Fri Jan 19, 2007 8:38 pm
- Please enter the next number in sequence: 1
- Location: In the dog house. Gone playing music too much recently.
- Contact:
Re: This Old Flute #2 - HF Meyer
I'm actually glad to hear you suggest filling the crack Jem, because that is my inclination. I don't like to do things that take a lot of force, following the motto "if you need to force it you are probably doing it wrong." Forging metal being the exception.
And Jon, the fissure (It's more than just a crack) is going to be impossible to get really clean, so any glue is going to have less than perfect conditions.
So, on those two pieces of advice, I think I'll go with CA glue and baking soda to fill the crack and embouchure hole then attempt to color match a skin coat of gel coat with a repair kit from West Marine. Unless of course some others report problems with that approach.
Sadly, the makers mark is on the head, aligned with the current embouchure, so it will drift around the head when I drill the new hole. So be it tho, as the crack does indeed go thru the embouchure wall and opens quite a lot there.
Here's a close-up of the rings...
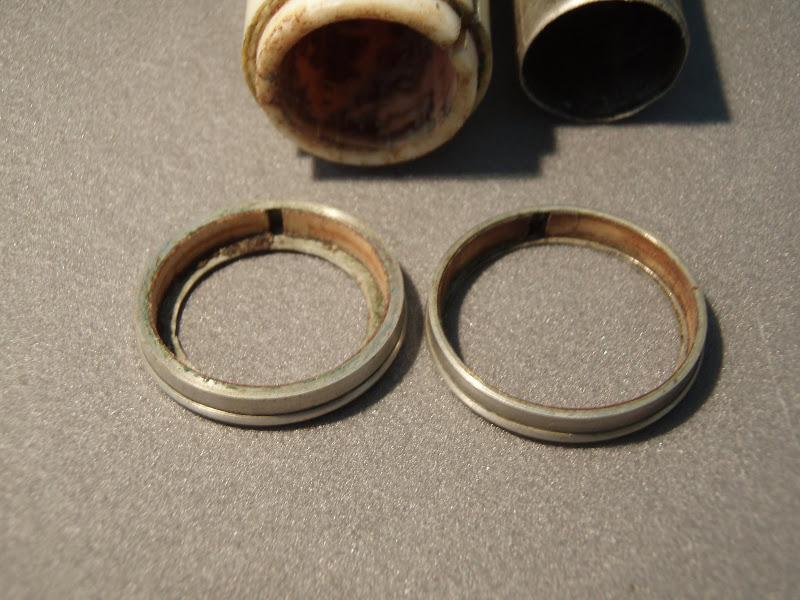

And Jon, the fissure (It's more than just a crack) is going to be impossible to get really clean, so any glue is going to have less than perfect conditions.
So, on those two pieces of advice, I think I'll go with CA glue and baking soda to fill the crack and embouchure hole then attempt to color match a skin coat of gel coat with a repair kit from West Marine. Unless of course some others report problems with that approach.
Sadly, the makers mark is on the head, aligned with the current embouchure, so it will drift around the head when I drill the new hole. So be it tho, as the crack does indeed go thru the embouchure wall and opens quite a lot there.
Here's a close-up of the rings...
When there's a huge spill of solar energy, it's just called a nice day.
http://www.parkswhistles.com
http://www.parkswhistles.com
- Jon C.
- Posts: 3526
- Joined: Wed Nov 07, 2001 6:00 pm
- antispam: No
- Please enter the next number in sequence: 8
- Tell us something.: I restore 19th century flutes, specializing in Rudall & Rose, and early American flutes. I occasionally make new flutes. Been at it for about 15 years.
- Location: San Diego
Re: This Old Flute #2 - HF Meyer
That is how my Meyers rings are, wood clad with metal.
"I love the flute because it's the one instrument in the world where you can feel your own breath. I can feel my breath with my fingers. It's as if I'm speaking from my soul..."
Michael Flatley
Jon
Michael Flatley
Jon
- Carey
- Posts: 578
- Joined: Fri Jan 19, 2007 8:38 pm
- Please enter the next number in sequence: 1
- Location: In the dog house. Gone playing music too much recently.
- Contact:
Re: This Old Flute #2 - HF Meyer
Well now I'm convinced it really is a Meyer. So that's what I'll call it.
When there's a huge spill of solar energy, it's just called a nice day.
http://www.parkswhistles.com
http://www.parkswhistles.com
- MarkP
- Posts: 859
- Joined: Tue Jun 26, 2007 5:49 am
- antispam: No
- Please enter the next number in sequence: 8
- Location: A long way from being an 'expert' at this
Re: This Old Flute #2 - HF Meyer
So here's an even more naive question. What's the best way to get the metal tube out of the barrel in the first place without creating even more damage? I have a cracked German flute that isn't worth much but would be a fun project to practice on. Barrel has a hairline split end to end and air escapes somewhere (possibly for the similar reason that the tube might not be complete inside) but it's a fine enough crack that it might mend. Is there a rough working guide on the web anywhere?I found a couple interesting things (interesting to me having never been here before. Others will have expected it.)
First, liner was at one time a flat piece of metal that was rolled and welded or soldered into a tube.
Mark
- Carey
- Posts: 578
- Joined: Fri Jan 19, 2007 8:38 pm
- Please enter the next number in sequence: 1
- Location: In the dog house. Gone playing music too much recently.
- Contact:
Re: This Old Flute #2 - HF Meyer
I'm not aware of any step-by-steps, but perhaps others here are. At this point it's broken field running for me. Each problem is a unique case and I have to proceed as the situation demands. Generally, step one is getting the rings off. Jon has suggested epoxying the rings to a metal plate while still attached to the joint and once hardened you can (usually?) tap the plate away from the joint and then after heating, chip the epoxy off the ring. Once the rings are off I'll usually make a plug for the liner and a sleve so I can get a grip on it and tap the barrel off the liner. Sometimes they just slide right out. Depends. I make good use of my lathe, drill press and band saw for making jigs and holding/clamping things. I don't think I'd be as brave if I only had a pair of pliers and a screw driver.
Wait, I think Terry McGee has something on his web site about cracked heads and barrels ... http://www.mcgee-flutes.com/headcrack.html check that out.
And cracked sockets too http://www.mcgee-flutes.com/cracked_sockets.html
Wait, I think Terry McGee has something on his web site about cracked heads and barrels ... http://www.mcgee-flutes.com/headcrack.html check that out.
And cracked sockets too http://www.mcgee-flutes.com/cracked_sockets.html
Last edited by Carey on Thu May 28, 2009 6:52 pm, edited 1 time in total.
When there's a huge spill of solar energy, it's just called a nice day.
http://www.parkswhistles.com
http://www.parkswhistles.com
- jemtheflute
- Posts: 6969
- Joined: Tue May 23, 2006 6:47 am
- antispam: No
- Please enter the next number in sequence: 8
- Location: N.E. Wales, G.B.
- Contact:
Re: This Old Flute #2 - HF Meyer
Mark, I think both Jon C and I have written various bits and bobs about methods we use/have tried here on C&F, though probably not a unified set of "destructions"! Use the search tool on appropriate keywords......
Head and barrel liner tubes are almost always a rolled and soldered tube, not an extruded or "drawn" seamless one - they didn't have the technology in the C19th, or at least not for aplication to flutes. I believe most metal Bohm flutes until well into the C20th were also made from seamed tube and that even when drawn tube became more available, it was seen as inferior..... Turning and drilling/reaming a liner tube from a lump of solid metal would not have been an economically viable option for the most part, though I have come across a couple of barrel mliners apparently done that way - much chunkier than usual and definitely seamless.
Most liner tubes were fixed in with shellac or an animal glue as well as having little keying punch-scuffs on their outer surface. It is usually necessary to apply heat to melt this in order to be able to pull the tube out of the wooden sleeve - which makes it a little awkward to do as the metal is rather thin and will be damaged if you try to grip and pull it with e.g. pliers. I have used those rubber tape grips that work in the fashion of a chain wrench with some success, but the hot metal isn't kind to the rubber! You don't have to worry too much about the wood when heating - it can take qiute a lot, so long as you don't actually scorch it. I use a paint-stripper hot air gun and blow the air through the tube from the tuning slide end trying not to aim it at the wood. This mostly suffices, though I have had some problems with stubborn ones from time to time.
BTW, I think it unlikely that there will be bits "missing" from the liner tube or that the soldered seam will have holes in it - I've not yet seen such. Carey was only saying that the embouchure hole in the liner tube was roughly cut out and didn't match the hole in the ivory, being raggedly bigger in places. This I can tell you is quite common, as indeed are poorly cut, assymetrical and squint embouchure holes, even on otherwise well made, good quality instruments! They don't seem normally to have installed the liner first and then drilled the embouchure through both layers as we might expect, but punched a relatively crude hole in the metal first and then not necessarily got it concentric with the hole in the wood/ivory, nor made it smaller than final size and filed it out for a clean finish....... Goodness knows why - that wouldn't have been beyond their technical ability!
If you only need to do a barrel, that is usually quite straightforward. The only awkward problem I've encountered there in a couple of German flutes is that the socket end of the liner tube was pressed out and back over the bore step between the socket and the narrower main section, while the top end, the protruding female part of the tuning slide was double layered above the wood with a second thickness soldered onto the tube outside the liner - making it impossible to pull the metal tube out in either direction! You have either to find a way to lift the crimped back bit in the socket, or accept deliberately cracking the wood a second time in order to break it off the liner. That actually isn't so terrible - it just means gluing it back together and getting a good finish on two cracks instead of one. If you can lift the folded metal that is preferable, though. It doesnt matter if you make a minor mess of the end of the liner tube - you can just file that bit away - it isn't necessary to fix it back in the same way as using a modern glue to reassemble things obviates that - and many flutes don't have that feature anyway, just a flush end of the liner tube at the socket bore-step.
As for removing ferrule rings, so far I have always done this by using the edge of my Opinel knife blade - very carefully at first cutting into the joint between metal and tube, then working them off by wiggling it and then angling it and pushing at the metal and working around and around, but being very careful not to chip the end grain of the wood. Carey's method would be good for a really stubborn one, I suppose, but mostly just isn't necessary.
Head and barrel liner tubes are almost always a rolled and soldered tube, not an extruded or "drawn" seamless one - they didn't have the technology in the C19th, or at least not for aplication to flutes. I believe most metal Bohm flutes until well into the C20th were also made from seamed tube and that even when drawn tube became more available, it was seen as inferior..... Turning and drilling/reaming a liner tube from a lump of solid metal would not have been an economically viable option for the most part, though I have come across a couple of barrel mliners apparently done that way - much chunkier than usual and definitely seamless.
Most liner tubes were fixed in with shellac or an animal glue as well as having little keying punch-scuffs on their outer surface. It is usually necessary to apply heat to melt this in order to be able to pull the tube out of the wooden sleeve - which makes it a little awkward to do as the metal is rather thin and will be damaged if you try to grip and pull it with e.g. pliers. I have used those rubber tape grips that work in the fashion of a chain wrench with some success, but the hot metal isn't kind to the rubber! You don't have to worry too much about the wood when heating - it can take qiute a lot, so long as you don't actually scorch it. I use a paint-stripper hot air gun and blow the air through the tube from the tuning slide end trying not to aim it at the wood. This mostly suffices, though I have had some problems with stubborn ones from time to time.
BTW, I think it unlikely that there will be bits "missing" from the liner tube or that the soldered seam will have holes in it - I've not yet seen such. Carey was only saying that the embouchure hole in the liner tube was roughly cut out and didn't match the hole in the ivory, being raggedly bigger in places. This I can tell you is quite common, as indeed are poorly cut, assymetrical and squint embouchure holes, even on otherwise well made, good quality instruments! They don't seem normally to have installed the liner first and then drilled the embouchure through both layers as we might expect, but punched a relatively crude hole in the metal first and then not necessarily got it concentric with the hole in the wood/ivory, nor made it smaller than final size and filed it out for a clean finish....... Goodness knows why - that wouldn't have been beyond their technical ability!
If you only need to do a barrel, that is usually quite straightforward. The only awkward problem I've encountered there in a couple of German flutes is that the socket end of the liner tube was pressed out and back over the bore step between the socket and the narrower main section, while the top end, the protruding female part of the tuning slide was double layered above the wood with a second thickness soldered onto the tube outside the liner - making it impossible to pull the metal tube out in either direction! You have either to find a way to lift the crimped back bit in the socket, or accept deliberately cracking the wood a second time in order to break it off the liner. That actually isn't so terrible - it just means gluing it back together and getting a good finish on two cracks instead of one. If you can lift the folded metal that is preferable, though. It doesnt matter if you make a minor mess of the end of the liner tube - you can just file that bit away - it isn't necessary to fix it back in the same way as using a modern glue to reassemble things obviates that - and many flutes don't have that feature anyway, just a flush end of the liner tube at the socket bore-step.
As for removing ferrule rings, so far I have always done this by using the edge of my Opinel knife blade - very carefully at first cutting into the joint between metal and tube, then working them off by wiggling it and then angling it and pushing at the metal and working around and around, but being very careful not to chip the end grain of the wood. Carey's method would be good for a really stubborn one, I suppose, but mostly just isn't necessary.
I respect people's privilege to hold their beliefs, whatever those may be (within reason), but respect the beliefs themselves? You gotta be kidding!
My YouTube channel
My FB photo albums
Low Bb flute: 2 reels (audio)
Flute & Music Resources - helpsheet downloads
My YouTube channel
My FB photo albums
Low Bb flute: 2 reels (audio)
Flute & Music Resources - helpsheet downloads
- Jon C.
- Posts: 3526
- Joined: Wed Nov 07, 2001 6:00 pm
- antispam: No
- Please enter the next number in sequence: 8
- Tell us something.: I restore 19th century flutes, specializing in Rudall & Rose, and early American flutes. I occasionally make new flutes. Been at it for about 15 years.
- Location: San Diego
Re: This Old Flute #2 - HF Meyer
ya, what he said...jemtheflute wrote:Mark, I think both Jon C and I have written various bits and bobs about methods we use/have tried here on C&F, though probably not a unified set of "destructions"! Use the search tool on appropriate keywords......
Head and barrel liner tubes are almost always a rolled and soldered tube, not an extruded or "drawn" seamless one - they didn't have the technology in the C19th, or at least not for aplication to flutes. I believe most metal Bohm flutes until well into the C20th were also made from seamed tube and that even when drawn tube became more available, it was seen as inferior..... Turning and drilling/reaming a liner tube from a lump of solid metal would not have been an economically viable option for the most part, though I have come across a couple of barrel mliners apparently done that way - much chunkier than usual and definitely seamless.
Most liner tubes were fixed in with shellac or an animal glue as well as having little keying punch-scuffs on their outer surface. It is usually necessary to apply heat to melt this in order to be able to pull the tube out of the wooden sleeve - which makes it a little awkward to do as the metal is rather thin and will be damaged if you try to grip and pull it with e.g. pliers. I have used those rubber tape grips that work in the fashion of a chain wrench with some success, but the hot metal isn't kind to the rubber! You don't have to worry too much about the wood when heating - it can take qiute a lot, so long as you don't actually scorch it. I use a paint-stripper hot air gun and blow the air through the tube from the tuning slide end trying not to aim it at the wood. This mostly suffices, though I have had some problems with stubborn ones from time to time.
BTW, I think it unlikely that there will be bits "missing" from the liner tube or that the soldered seam will have holes in it - I've not yet seen such. Carey was only saying that the embouchure hole in the liner tube was roughly cut out and didn't match the hole in the ivory, being raggedly bigger in places. This I can tell you is quite common, as indeed are poorly cut, assymetrical and squint embouchure holes, even on otherwise well made, good quality instruments! They don't seem normally to have installed the liner first and then drilled the embouchure through both layers as we might expect, but punched a relatively crude hole in the metal first and then not necessarily got it concentric with the hole in the wood/ivory, nor made it smaller than final size and filed it out for a clean finish....... Goodness knows why - that wouldn't have been beyond their technical ability!
If you only need to do a barrel, that is usually quite straightforward. The only awkward problem I've encountered there in a couple of German flutes is that the socket end of the liner tube was pressed out and back over the bore step between the socket and the narrower main section, while the top end, the protruding female part of the tuning slide was double layered above the wood with a second thickness soldered onto the tube outside the liner - making it impossible to pull the metal tube out in either direction! You have either to find a way to lift the crimped back bit in the socket, or accept deliberately cracking the wood a second time in order to break it off the liner. That actually isn't so terrible - it just means gluing it back together and getting a good finish on two cracks instead of one. If you can lift the folded metal that is preferable, though. It doesnt matter if you make a minor mess of the end of the liner tube - you can just file that bit away - it isn't necessary to fix it back in the same way as using a modern glue to reassemble things obviates that - and many flutes don't have that feature anyway, just a flush end of the liner tube at the socket bore-step.
As for removing ferrule rings, so far I have always done this by using the edge of my Opinel knife blade - very carefully at first cutting into the joint between metal and tube, then working them off by wiggling it and then angling it and pushing at the metal and working around and around, but being very careful not to chip the end grain of the wood. Carey's method would be good for a really stubborn one, I suppose, but mostly just isn't necessary.
I just knock the rings off with a block of wood and a hammer. If they are flush, then it is more of a problem.
"I love the flute because it's the one instrument in the world where you can feel your own breath. I can feel my breath with my fingers. It's as if I'm speaking from my soul..."
Michael Flatley
Jon
Michael Flatley
Jon
- Carey
- Posts: 578
- Joined: Fri Jan 19, 2007 8:38 pm
- Please enter the next number in sequence: 1
- Location: In the dog house. Gone playing music too much recently.
- Contact:
Re: This Old Flute #2 - HF Meyer
OK, some progress last night. Not much to report however, since I just pulled all the keys off and bagged them with their axles for future cleaning and reassembly. Then I set about cleaning the body. Lots of gunk had collected under and around the keys and posts as well as in the pad seats. So I put some tunes on the mp3 player and set about scraping and brushing.
One thought did strike me while I was cleaning the head wondering how much I was going to have to shorten this one to get A=440. Hey! Since I'm thinking I'll drill a new embouchure, I can drill it wherever I like and I don't have to hack on the head length. Hmm... that would mean elongating the hole in the metal liner or making a second one, but that's not the end of the world. Or I could fill and drill the embouchure in the current position, or adjusted slightly.
I think I'll finish cleaning out the head joint and then fill in the crack and embouchure well enough to evaluate the tuning of the original configuration once I have it re-corked and see where I want to go after that.
One thought did strike me while I was cleaning the head wondering how much I was going to have to shorten this one to get A=440. Hey! Since I'm thinking I'll drill a new embouchure, I can drill it wherever I like and I don't have to hack on the head length. Hmm... that would mean elongating the hole in the metal liner or making a second one, but that's not the end of the world. Or I could fill and drill the embouchure in the current position, or adjusted slightly.
I think I'll finish cleaning out the head joint and then fill in the crack and embouchure well enough to evaluate the tuning of the original configuration once I have it re-corked and see where I want to go after that.
When there's a huge spill of solar energy, it's just called a nice day.
http://www.parkswhistles.com
http://www.parkswhistles.com
- Carey
- Posts: 578
- Joined: Fri Jan 19, 2007 8:38 pm
- Please enter the next number in sequence: 1
- Location: In the dog house. Gone playing music too much recently.
- Contact:
Re: This Old Flute #2 - HF Meyer
More progress today. After chasing whistles around two counties I came home to a thunderstorm and rather that risk working on the lathe when the power could go out I set about more flute work. Finished the corks, taped up the holes where all the keys used to be, and had a toot with the flute left-handed, so I was blowing on the un-cracked edge of the embouchure.
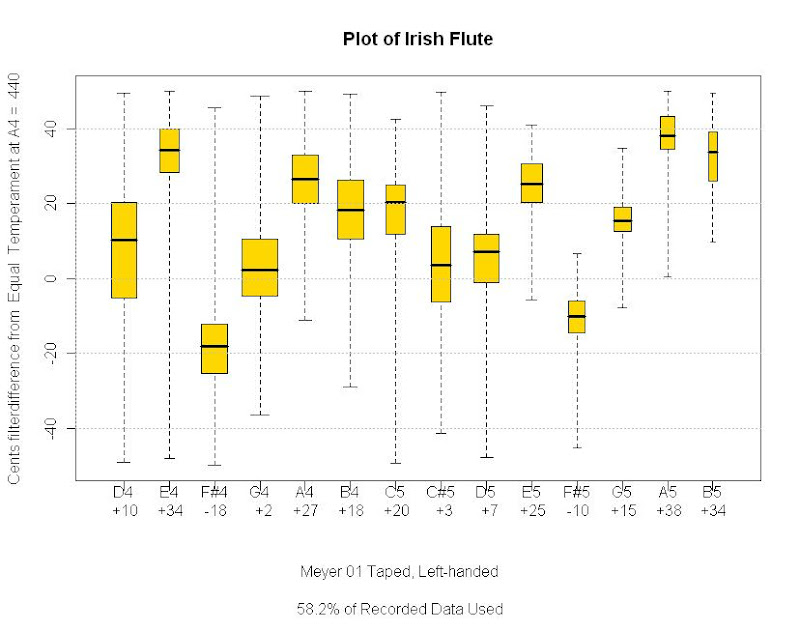
Pretty ugly, but I don't know how much faith I put in that plot. I was having a hard time playing the flute left-handed. But even so, except for the flat F# (am I supposed to vent that?) it's withing +/- 20 cents. I thought the tone was surprisingly good in the upper half of the first octave. I should have had a video going when I blew the first note. I would have like to have seen my face.
The two octaves have the same pattern, so there's hope for bringing it nicely into tune with less work than my nach Meyer (viewtopic.php?f=2&t=61643)
Here's a shot of the flute as played.

And one of the head joint.
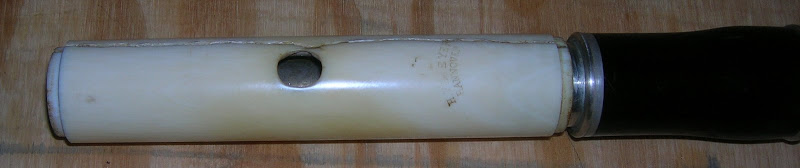
See the crack ruined the blowing edge? I think I'll just fill in the crack and then have a go and see what I've got. It looks like the flute might be A=440. Thoughts Graeme and Terry? I think I'll go get a gel coat patch kit and mix up some gel coat to match and see how it comes out. The crack was pretty dirty with old glue so I used a Dremel tool with the dentist type bit to clean out the crack. I spun a dowel with emery cloth on the end to clean the glue out of the ivory head. The liner now fits nice and snug but can be moved if you want. I'll leave it that way for now.
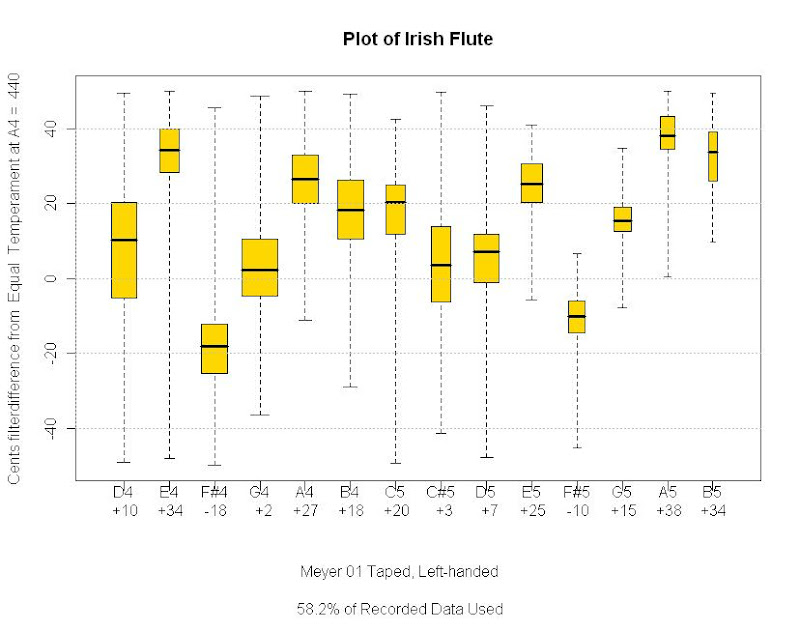
Pretty ugly, but I don't know how much faith I put in that plot. I was having a hard time playing the flute left-handed. But even so, except for the flat F# (am I supposed to vent that?) it's withing +/- 20 cents. I thought the tone was surprisingly good in the upper half of the first octave. I should have had a video going when I blew the first note. I would have like to have seen my face.
The two octaves have the same pattern, so there's hope for bringing it nicely into tune with less work than my nach Meyer (viewtopic.php?f=2&t=61643)
Here's a shot of the flute as played.
And one of the head joint.
See the crack ruined the blowing edge? I think I'll just fill in the crack and then have a go and see what I've got. It looks like the flute might be A=440. Thoughts Graeme and Terry? I think I'll go get a gel coat patch kit and mix up some gel coat to match and see how it comes out. The crack was pretty dirty with old glue so I used a Dremel tool with the dentist type bit to clean out the crack. I spun a dowel with emery cloth on the end to clean the glue out of the ivory head. The liner now fits nice and snug but can be moved if you want. I'll leave it that way for now.
When there's a huge spill of solar energy, it's just called a nice day.
http://www.parkswhistles.com
http://www.parkswhistles.com