Both whistles are stunning pieces of craftsmanship from a wood working standpoint. I have seen no other low whistles made for playing Irish style music that could compete with these on a visual level – real eye candy they are.
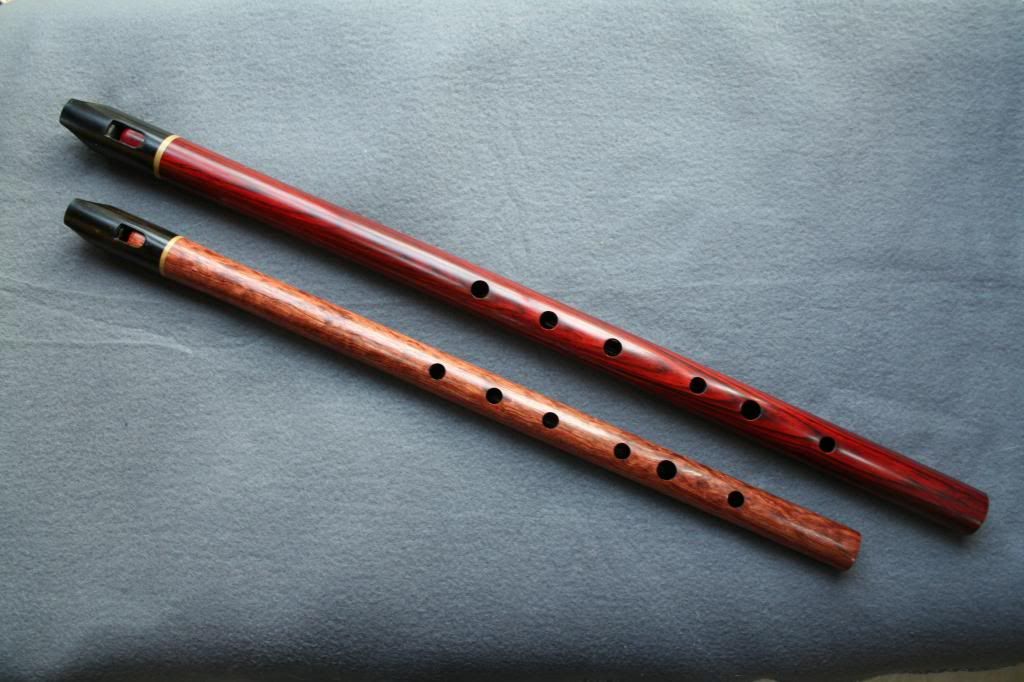
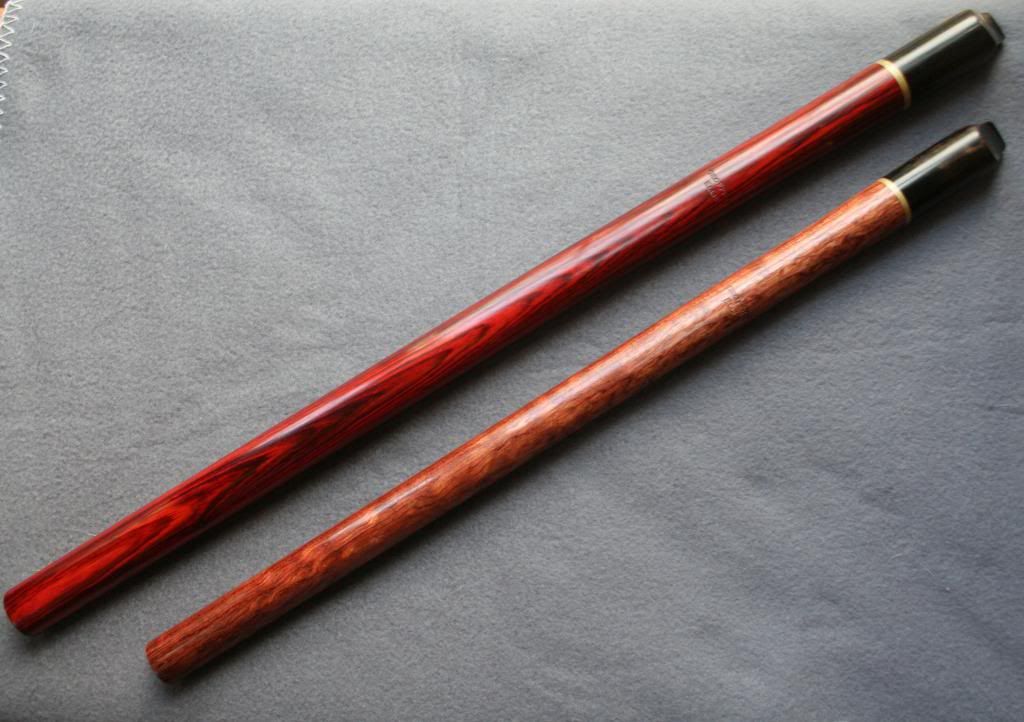
One whistle is a low F whistle made from waterfall bubinga. The chatoyance of the bubinga is mesmerizing. The other is a low D made from cocobolo. Both have an outer mouthpiece made from ebony. The plug is also ebony as far as I can tell. The whistles are all wood except for a small band of gold colored filler (powdered brass says Geoffrey) inlaid where the outer mouthpiece meets the body of the whistle. The design is one piece and the tuning is fixed.
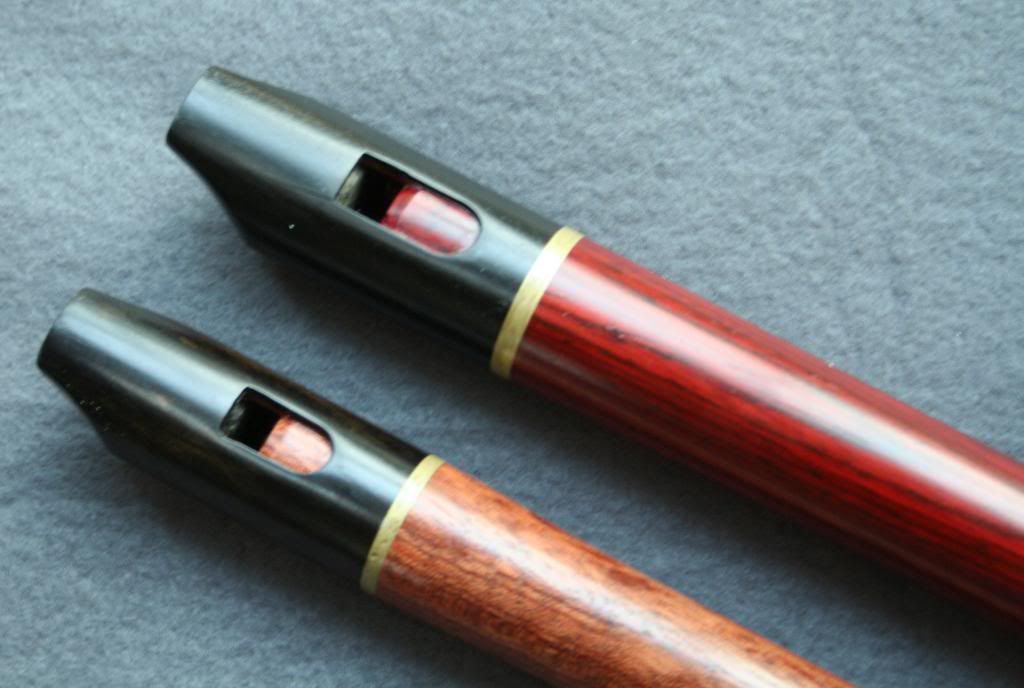
The general format of the whistle borrows some ideas from the MK style of low whistle. The body is one long length of wooden tube. A tenon is turned at the top of the tube and the windway and labium are cut into that. The outer mouthpiece slips over the tenon and incorporates the voicing window. I imagine that this arrangement allows the maker to voice each whistle to his liking leaving a bit of a gap below the mouthpiece. That gap gets filled with the brass inlay material once voiced. The wooden tubing is quite thin walled and that makes for a very lightweight whistle. I have some idea just how hard it is to make such a thin wall such as these and I am impressed with the craftsmanship of these instruments.
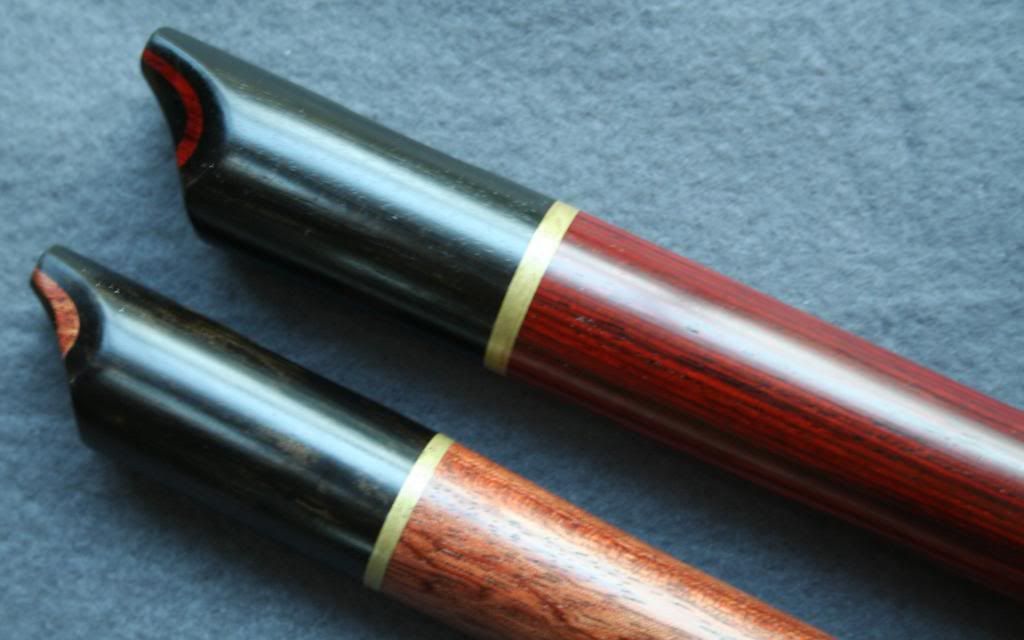
The mouthpiece is shaped in an interesting and somewhat unique manner. Just as the beak of an MK is milled from the sides to reduce the size of the beak so is the Ellis whistle. But the angle is rather unique and does not leave a sharp edge under the center of the beak. It is all smooth as can be. The mouthpiece is a bit chunky compared to some whistles but provided you just rest it on your lips it is quite comfortable and easy to become accustomed to.
The voice of each Ellis whistle is quite husky. As I play each of these find myself thinking just how "woody" these things sound. The timbre is very warm. There is a lot of air in the tone to. I like it.
Breath requirements are medium and the blowing pressure is moderate as well. Hole sizing and placement is certainly similar to most good low whistles – you know, the Goldilocks size – not too large, not too small. I felt no need to stretch my grip. I did not observe any issues with constrained venting at all. Response is good and I find these whistle easy to play. You do not have to consciously push the top notes until you get to the third octave note. The high B (D whistle terminology) on the low F was a little harder to hit than it was on the low D. That’s the only playing difference I observed between the two whistles. YMMV
Tuning is fixed as I said above. Each whistle sounds in tune with itself playing alone. I did not put them to a tuner. I did record some samples to scratch tracks I had on hand which are spot on concert pitch. You can judge the tuning against those yourself. I do notice that I play a few notes a bit flat on the low D. That may be my inexperience with the whistle. So let’s see what other players think. I like tuning slides personally but I realize that a whistle can be made that plays in tune at concert pitch. So unless you play with one of those fiddlers that likes to tune flat or play sharp everything should be copasetic. Geoffrey has informed me that he is working on a model with a tuning slide which will be available in the future.
Here are some sound samples of each whistle. These were done quickly accompanied by tracks I already had on hand. Three of the four tunes are my own - any resemblance to other tunes living or dead is strictly a coincidence. My playing is not perfect but you can hear the tone of the whistles.
Low F first.
https://www.box.com/s/2qp0g67wx1mhcf8rx6ll
https://www.box.com/s/xutkptt4s87vu8ufyfk3
https://www.box.com/s/a68n026x6z1ssc601iz1 without any accompniment
Low D, last but not least.
https://www.box.com/s/671pjyp856q6ujk254ri
https://www.box.com/s/lbest23uqbga67u40zit
All in all, I like these whistles a lot. I enjoyed playing them and I would like to thank Geoffrey Ellis for sending these out on tour. If you are looking for a unique whistle, and you like exotic woods, these are just the ticket.
Thanks Geoffrey.
Feadoggie