Cutting the soundblade
- MadmanWithaWhistle
- Posts: 697
- Joined: Fri Jan 27, 2012 10:15 pm
- antispam: No
- Please enter the next number in sequence: 8
- Tell us something.: Instrument maker and researcher exploring new methods of creating traditional instruments with longevity aforethought. Player of the whistle, flute, and continental European border pipes.
Cutting the soundblade
Hi,
I wondered what techniques any whistlemakers who use curved windways have come up with in terms of a repeatable way of cutting the soundblade after making the headjoint blank. Making a jig for a dremel or hand-filing it sounds tedious and difficult to repeat. The undercut I'm testing will need to be done by hand, but that's no more than a few strokes of the file.
Thanks for sharing your thoughts!
I wondered what techniques any whistlemakers who use curved windways have come up with in terms of a repeatable way of cutting the soundblade after making the headjoint blank. Making a jig for a dremel or hand-filing it sounds tedious and difficult to repeat. The undercut I'm testing will need to be done by hand, but that's no more than a few strokes of the file.
Thanks for sharing your thoughts!
Re: Cutting the soundblade
I do all of mine with simple eye hand coordination. Good files, and a vice with soft enough V blocks to hold the whistle head steady witout having to steady it with a hand. Good lighting is also important. Using both hands to press, and steer the files cuts down on hand fatigue. My small vice is mounted on a pipe with a clamp that allows me to work standing or sitting. When making ''Whistles of Wood'' I do use some wood carving tools to remove some of the wood then switch to files for the intricut diminsions. Let go of the idea that it takes a square file to make a good cornor cut.MadmanWithaWhistle wrote:Hi,
I wondered what techniques any whistlemakers who use curved windways have come up with in terms of a repeatable way of cutting the soundblade after making the headjoint blank.
Making a jig for a dremel or hand-filing it sounds tedious and difficult to repeat.
The undercut I'm testing will need to be done by hand, but that's no more than a few strokes of the file.
Thanks for sharing your thoughts!
trying to make a square cornor with a square file will not let you see in the cornor because it is covered with the file.
Use a triangle or three square file. This will allow seeing the sides alternatley, and allow getting into the cornor to make a real nice sharp cornor. It does not have to be a sharp cornor to whistle good but pepoel expect to see things that mark quality.
You will need to try some differant files to find out what you like best. Mill files only cut in one direction, and it is hard to find good ones small enough. I prefer the small diamond coated files that cut in both directions. Being able to cut in both directions helps to eliminat hanging chaff of wood or plastic. I could go on and on but I think this is enough to get you started.
Think about all the things you do using eye hand cordination then dive in. Pencil markes may help at first but when you do a lot of them the marks will fade away.
''Whistles of Wood'', cpvc and brass. viewtopic.php?f=1&t=69086
- MadmanWithaWhistle
- Posts: 697
- Joined: Fri Jan 27, 2012 10:15 pm
- antispam: No
- Please enter the next number in sequence: 8
- Tell us something.: Instrument maker and researcher exploring new methods of creating traditional instruments with longevity aforethought. Player of the whistle, flute, and continental European border pipes.
Re: Cutting the soundblade
Thanks for the tip, Tommy. I'm making these out of brass, if that makes a difference. Maybe the way to go is to make initial cuts with a dremel and then finish with a file?
- brewerpaul
- Posts: 7300
- Joined: Wed Jun 27, 2001 6:00 pm
- antispam: No
- Please enter the next number in sequence: 10
- Location: Clifton Park, NY
- Contact:
Re: Cutting the soundblade
I do mine all by hand with a file given to me by Glenn Schultz. It's a triangle file with two smooth sides. I start with one of the smooth sides vertical against the right side of the blade. When I get that close to the correct depth, I do the same with the left side vertical. Next, the rough side in the middle of the blade. Then I file the areas between those three flats. This gives the rough blade shape which I then refine bit by bit using the same file, sometimes finishing with fine diamond files
- MadmanWithaWhistle
- Posts: 697
- Joined: Fri Jan 27, 2012 10:15 pm
- antispam: No
- Please enter the next number in sequence: 8
- Tell us something.: Instrument maker and researcher exploring new methods of creating traditional instruments with longevity aforethought. Player of the whistle, flute, and continental European border pipes.
Re: Cutting the soundblade
Thanks Paul. I'll look at the files available and see if I can use or adapt that technique. First shop day is tomorrow. I'm very curious to see what I come up with.brewerpaul wrote:I do mine all by hand with a file given to me by Glenn Schultz. It's a triangle file with two smooth sides. I start with one of the smooth sides vertical against the right side of the blade. When I get that close to the correct depth, I do the same with the left side vertical. Next, the rough side in the middle of the blade. Then I file the areas between those three flats. This gives the rough blade shape which I then refine bit by bit using the same file, sometimes finishing with fine diamond files
- brewerpaul
- Posts: 7300
- Joined: Wed Jun 27, 2001 6:00 pm
- antispam: No
- Please enter the next number in sequence: 10
- Location: Clifton Park, NY
- Contact:
Re: Cutting the soundblade
That smooth sided file is elusive. In fact, some Google searching didn't find ANY for sale! Since he was a machinist, I'm thinking that Glenn smoothed out those two sides himself. Once I unpack my tools I'll have to look more closely.
I did find references to smoothing a side of a file on a belt sander, and I'd imagine a grinding wheel would work too.
With care, you can probably get away with a regular triangle file. The smooth sides are to protect the sides of the "window".
I did find references to smoothing a side of a file on a belt sander, and I'd imagine a grinding wheel would work too.
With care, you can probably get away with a regular triangle file. The smooth sides are to protect the sides of the "window".
- hans
- Posts: 2259
- Joined: Fri Nov 01, 2002 6:00 pm
- antispam: No
- Please enter the next number in sequence: 8
- Tell us something.: I've been making whistles since 2010 in my tiny workshop at my home. I've been playing whistle since teenage times.
- Location: Moray Firth, Scotland
- Contact:
Re: Cutting the soundblade
Working with aluminium tubing, I first mark, then cut the windway slot into the head tube piece, using a fine hacksaw. The wind channel is slightly wider at the mouth end than the window end, cutting by hand with the tube hold at 45° in a vice with soft grips helps. Then I break the piece out by hand, not having cut or drilled at the window. I then proceed to file the blade to its final shape, from this rough state of being broken off. Maybe this is slightly tedious, but I do not mind. I know what shape I am after, and find this easier to achieve entirely by hand. I adjust the width of the window at the same time. I use three types of semi-round quality Swiss needle files: Bahco 304-16-0 (bast.ard), Bahco 304-14-2 (smooth) and Bahco 304-16-4 (dead smooth), all mounted in wooden handles. The Bahco smooth and dead smooth semi-round files are probably the most used tools in my workshop.MadmanWithaWhistle wrote:I wondered what techniques any whistlemakers who use curved windways have come up with in terms of a repeatable way of cutting the soundblade after making the headjoint blank. Making a jig for a dremel or hand-filing it sounds tedious and difficult to repeat.
http://www.snaponindustrialbrands.com/c ... needle.htm
- syn whistles
- Posts: 319
- Joined: Tue Apr 01, 2003 1:55 pm
- antispam: No
- Please enter the next number in sequence: 8
- Location: st georges basin, australia
Re: Cutting the soundblade
If you are thinking about accuracy and repeatability, you should be thinking about machining rather than hand cutting or filing. When I look at John Sindt's work, it suggests to me that he uses a horizontal milling machine. Also some of the Alba whistles, but I suspect a different approach with the same type of machine. I use a milling machine too, but quite a different style.
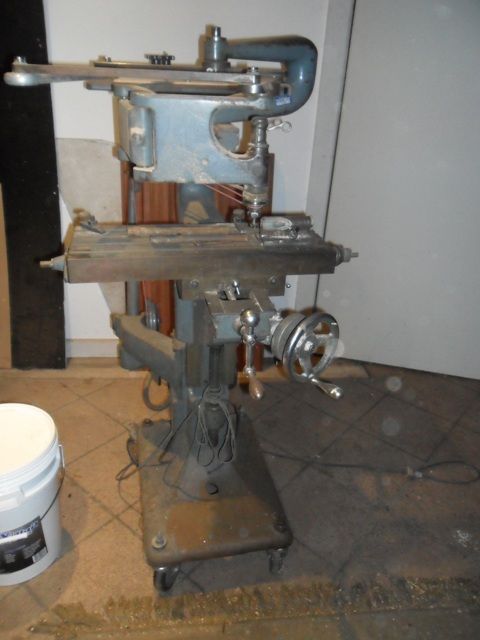
This is an engravers pantograph, largely redundant these days with the introduction of laser engravers and the like, and often available at quite a reasonable price. They function quite well as a mill, especially as they can move around in the horizontal plane and follow a pattern.
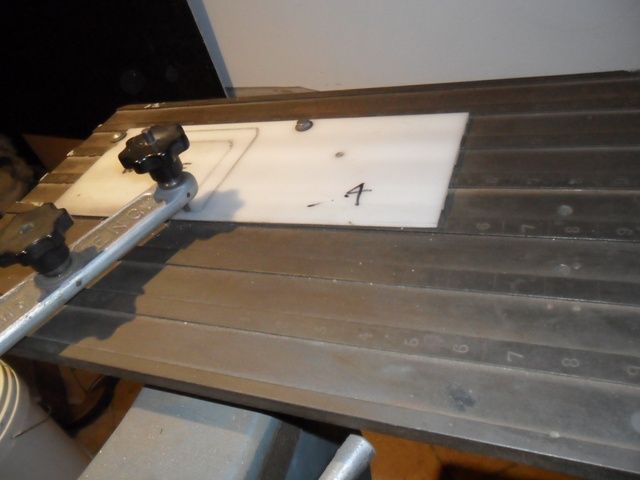
Here's the pattern I use to cut the windway and ramp in one operation. You can't see the tapering section of the pattern that comes out of the straight windway guide to give the angle of the ramp.
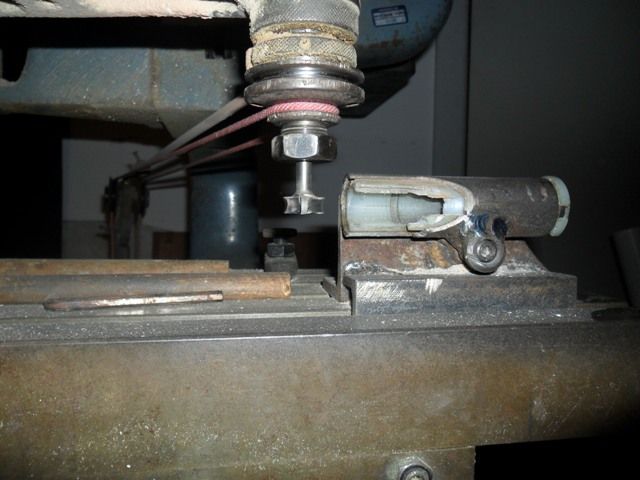
And here's the business end. The whistle head is clamped into the horizontal jig and the cutter moves horizontally, cutting the windway and then coming out of the job at an angle to create the ramp. The trickiest part is designing the cutter profile so that when it leaves the windway it presents a square finish to the bottom of the ramp rather than a curved one which will need a lot of file work to square up. I still use a file, but more for beburring than shaping.
Very accurate, very repeatable and a fair leeway for experiment with windway width and ramp angle once you are familiar with the machine.
I use another similar type of machine for milling fingerholes as drilling aluminium gives rather less than perfectly round results and it is quite easy to produce 'in-between' size holes.
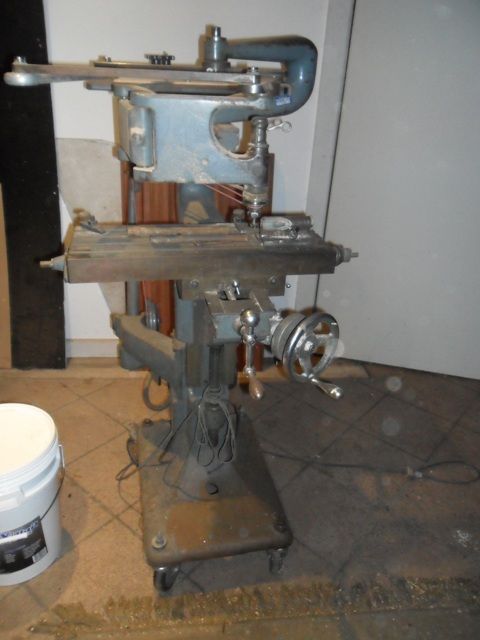
This is an engravers pantograph, largely redundant these days with the introduction of laser engravers and the like, and often available at quite a reasonable price. They function quite well as a mill, especially as they can move around in the horizontal plane and follow a pattern.
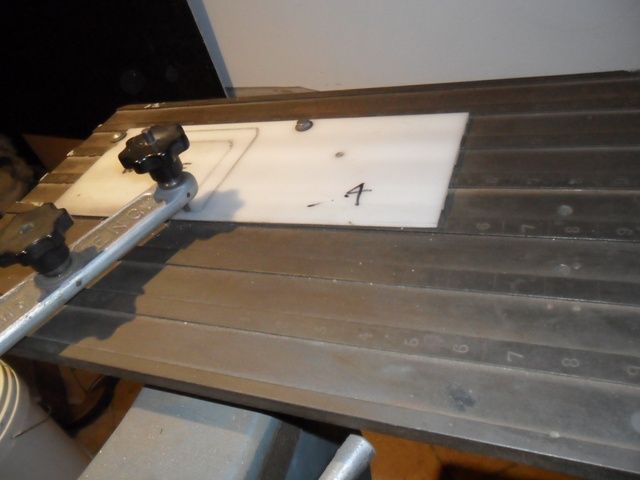
Here's the pattern I use to cut the windway and ramp in one operation. You can't see the tapering section of the pattern that comes out of the straight windway guide to give the angle of the ramp.
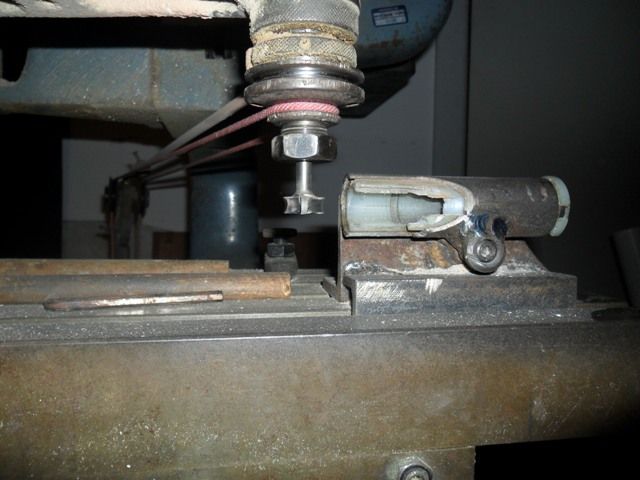
And here's the business end. The whistle head is clamped into the horizontal jig and the cutter moves horizontally, cutting the windway and then coming out of the job at an angle to create the ramp. The trickiest part is designing the cutter profile so that when it leaves the windway it presents a square finish to the bottom of the ramp rather than a curved one which will need a lot of file work to square up. I still use a file, but more for beburring than shaping.
Very accurate, very repeatable and a fair leeway for experiment with windway width and ramp angle once you are familiar with the machine.
I use another similar type of machine for milling fingerholes as drilling aluminium gives rather less than perfectly round results and it is quite easy to produce 'in-between' size holes.
So good it has to be a SYN!
- MadmanWithaWhistle
- Posts: 697
- Joined: Fri Jan 27, 2012 10:15 pm
- antispam: No
- Please enter the next number in sequence: 8
- Tell us something.: Instrument maker and researcher exploring new methods of creating traditional instruments with longevity aforethought. Player of the whistle, flute, and continental European border pipes.
Re: Cutting the soundblade
Thanks all for the background and info. I will indeed be milling the soundblade eventually with minor adjustments made with sandpaper afterward. Time for some math! I have successfully created a lovely headjoint by hand and will be making a second (mostly to correct some minor errors). Closing in on the sound I want steadily.This is the first real whistle I've made but reading the C&F threads on whistle physics etc for years beforehand certainly helped!
Very excited to debut these on a tour at some point and see what you folks think. You've been very gracious with your time and I appreciate it.
Very excited to debut these on a tour at some point and see what you folks think. You've been very gracious with your time and I appreciate it.
- Mitch
- Posts: 1826
- Joined: Tue Dec 20, 2005 6:58 pm
- antispam: No
- Please enter the next number in sequence: 8
- Location: Wombatistan
- Contact:
Re: Cutting the soundblade
I use a jig to pass-through a routing bit mounted on my mill.MadmanWithaWhistle wrote:Hi,
I wondered what techniques any whistlemakers who use curved windways have come up with in terms of a repeatable way of cutting the soundblade after making the headjoint blank. Making a jig for a dremel or hand-filing it sounds tedious and difficult to repeat. The undercut I'm testing will need to be done by hand, but that's no more than a few strokes of the file.
Thanks for sharing your thoughts!
As Erle suggests, the profile of the router/milling bit is not exactly circular so you have to do some sums to achieve the correct ellipse.
Wood is a bit more easy for final-tolerances, so I cut a little short and complete with blades and files.
This will be a lot harder with metal, and a good accurate mill will be a blessing.
I find that my run-out gauge is also a blessing for this work!
As you probably already know, the angle in the corners of a curved ramp is less than 90-degrees, so final finishing (if needed) has to be done with a triangle-file or similar. This depends on your design, but I assume radially parallel "ears" (in pipe-organ-speak).
One can grind a side off a triangle-file with a tool-grade stone on a bench grinder - might wreck a few files in the process, but well worth the effort.
For repeat-ability, jigs are a good investment to save time, but always measure, measure, measure.
(I have grown quite fond of Jigs in both the making and the playing

I look forward to your result!
- Latticino
- Posts: 445
- Joined: Tue Aug 05, 2008 7:30 pm
- antispam: No
- Please enter the next number in sequence: 8
- Location: Upstate NY
Re: Cutting the soundblade
[quote="Mitch"]
One can grind a side off a triangle-file with a tool-grade stone on a bench grinder - might wreck a few files in the process, but well worth the effort.
[quote]
When grinding the sides off jewelers files it is crucial to keep the file below the tempering temperature or you will ruin the heat treatment on the file and make all the teeth soft. Work slowly, don't try to hog off all the teeth at once and cool it regularly in water (dry at completion of course to avoid rust). If the file gets too hot to touch or starts to change colors you have most likely ruined it. Fortunately Harbor Freight has inexpensive jewelers files to experiment with before you kill your vintage Sandvik machinist set.
One can grind a side off a triangle-file with a tool-grade stone on a bench grinder - might wreck a few files in the process, but well worth the effort.
[quote]
When grinding the sides off jewelers files it is crucial to keep the file below the tempering temperature or you will ruin the heat treatment on the file and make all the teeth soft. Work slowly, don't try to hog off all the teeth at once and cool it regularly in water (dry at completion of course to avoid rust). If the file gets too hot to touch or starts to change colors you have most likely ruined it. Fortunately Harbor Freight has inexpensive jewelers files to experiment with before you kill your vintage Sandvik machinist set.
"Experience is something you don't get until just after you need it"
Steven Wright
"Your reality, sir, is lies and balderdash and I'm delighted to say that I have no grasp of it whatsoever."
Baron Munchausen
Steven Wright
"Your reality, sir, is lies and balderdash and I'm delighted to say that I have no grasp of it whatsoever."
Baron Munchausen
- MadmanWithaWhistle
- Posts: 697
- Joined: Fri Jan 27, 2012 10:15 pm
- antispam: No
- Please enter the next number in sequence: 8
- Tell us something.: Instrument maker and researcher exploring new methods of creating traditional instruments with longevity aforethought. Player of the whistle, flute, and continental European border pipes.
Re: Cutting the soundblade
Thanks all for the input. Thankfully I've actually killed two birds with one stone- after some experimentation a straight airblade proved easier to create, the crescent-shaped inset has the sound I want while still allowing every part of the curved windway to intersect with the blade. Way easier than trying for a curved windway anyway. I did arse up the outer diameter of the tubing (partly manufacturer's fault, partly mine) so the airblade angle is kind of shallow. I will correct that on the next go-round as well as trying to inset a sleeve of plastic or teflon in the part of the headjoint that accepts the body tube so there's no metal-metal contact. (My teacher is still unable to get the joint of her old Sindt apart).
- Daniel_Bingamon
- Posts: 2227
- Joined: Wed Jun 27, 2001 6:00 pm
- antispam: No
- Location: Kings Mills, OH
- Contact:
Re: Cutting the soundblade
I usually file blades on handmade whistles. I usually use a file and pinch my fingers between the limits of where it should be made.
However, there was an experiment I did once that could work.
1. You mount the headjoint of the whistle in a lathe (metal working lathe, not wood type)
2. Attach a flexible shaft dremal tool into the toolpost of the lathe.
3. Find a nice bit cutter bit that will fit into the end of the flexible shaft.
4. Tilt the toolpost to the desired angle. Turn the dremal to a reasonable cutting speed.
5. Most the toolpost into position.
6. Manually rotate the lathe spindle between the two ends of the desired area to be cut.
(I'm sure a jig *not the musical type* could be made to control the positions of the cut.
Someone could probably build a gadget to do that if they wanted to.
However, there was an experiment I did once that could work.
1. You mount the headjoint of the whistle in a lathe (metal working lathe, not wood type)
2. Attach a flexible shaft dremal tool into the toolpost of the lathe.
3. Find a nice bit cutter bit that will fit into the end of the flexible shaft.
4. Tilt the toolpost to the desired angle. Turn the dremal to a reasonable cutting speed.
5. Most the toolpost into position.
6. Manually rotate the lathe spindle between the two ends of the desired area to be cut.
(I'm sure a jig *not the musical type* could be made to control the positions of the cut.
Someone could probably build a gadget to do that if they wanted to.
- MadmanWithaWhistle
- Posts: 697
- Joined: Fri Jan 27, 2012 10:15 pm
- antispam: No
- Please enter the next number in sequence: 8
- Tell us something.: Instrument maker and researcher exploring new methods of creating traditional instruments with longevity aforethought. Player of the whistle, flute, and continental European border pipes.
Re: Cutting the soundblade
Productive day on Saturday. The steeper ramp and greater windway height helped immensely, and I ended up with a whistle I would be perfectly happy to play, but was just a little off from what I am seeking response-wise. As I experimented with adjusting the blade undercut and window length, I noticed that the Ds in both octaves became somewhat louder than the rest of the notes. Now, that could well end up being a "feature" but I didn't quite get to the level of "chirp" or "snap" I wanted either before overdoing it on filing the soundblade and moving farther from my intended sound. I may try a still-steeper ramp and try to introduce some "purposeful inconsistency" into the edge of the soundblade as well on the next go round. Thanks all for your support and input!